- Прессование пеллет: процесс и параметры
- Завод по производству пеллет для малого бизнеса не требует больших инвестиций
- На заводе должны производиться качественные пеллеты
- Технология производства пеллет для малого завода
- Заводу нужно поставить прессовочное оборудование
- Потребность в пеллетах все больше испытывают альтернативные отопительные системы
- Пеллетами можно заправлять автомобили
- Пеллеты использую как топливо для электростанций
- хорошая технология всегда в цене
- пеллеты и брикеты из отходов, биоэтанол и биодизель
- виды сырья, технологический процесс :: BusinessMan.ru
- изготовление и расход пеллет из древесных опилок
- Оборудование для производства пеллет
Прессование пеллет: процесс и параметры
Здравствуйте уважаемые читатели Блога Андрея Ноака! Более четырех лет я работал технологом на участке по производству пеллет, как и другие технологии переработки древесины на пеллетах имеется множество хитростей, зная которые можно достичь успеха в их изготовлении. Самыми главными тонкостями процесса производства пеллет я и хочу поделиться с моими читателями. Я хочу рассказать как делается прессование пеллет. Но качественное прессование не будет сделано без полного соблюдения технологического процесса.
Введение
Сегодня идет речь о полной и глубокой переработке древесины, и особенно актуальным является вопрос по утилизации отходов деревообработки. Я считаю что одной из самых наилучших технологий переработки древесных отходов является — производство пеллет. Вот несколько критериев по которым данная технология переработки отходов превосходит другие:
- Технология довольно проста.
- Для обслуживания работы оборудования необходимо минимальное количество персонала.
- Себестоимость производства довольно небольшая, а вот отдача от бизнеса высокая.
- Возможность переработки отходов различных размеров.
В одной из своих статей я даже сравнивал бизнес по производству дсп и пеллет, при этом пеллеты по большинству критериев остались в выигрыше, подробнее ознакомиться с статьей. Но как мы уже знаем, чтобы эффективно работать, необходимо знать технологию производства продукции от А до Я. И здесь к технологии производства относится:
- Сырье, с его размерами и влажностью.
- Процесс работы оборудования и режимы работы.
- Качество получаемых пеллет.
- Правильная упаковка пеллет.
При этом в интернете имеется достаточно большое количество информации про оборудования различных фирм. Но вот как работать на таком оборудовании никто не говорит, какое сырье предпочтительнее, какие нормы расхода сырья, как увеличить ресурс работы линии.
Проработав достаточно длительное время на производстве я видел, как иностранные специалисты приезжают и рассказывают за большие деньги, что будет ниже написано, и наверное это будет не совсем справедливо, ведь это просто обычная информация. Именно поэтому на своем блоге решил рассказать все о производстве пеллет.
Сырье для производства пеллет
Сырьем для пеллет является измельченная древесина размером около 1 мм толщиной и до 3-4 мм длиной. Преимуществом производства пеллет является тот факт, что здесь не требуется специально подготовленная стружка как к примеру для дсп. В сырье не допускается наличие минеральных примесей и металлических включений. Сырье для производства пеллет оказывает влияние на цвет готовых гранул:
- Черные пеллеты получают из древесины с наличием коры, и возможным наличием гнили.
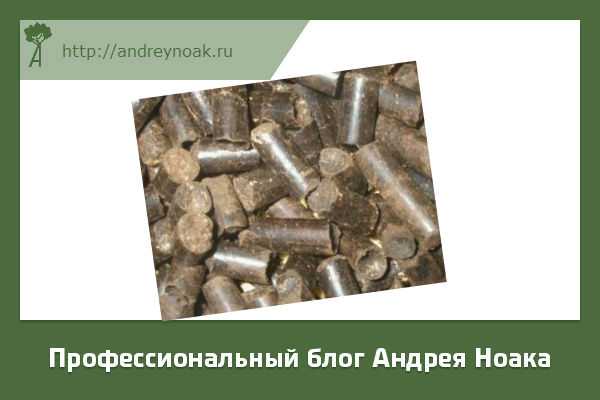
На фото черный пеллет, самый низкосортный. Черные пеллеты, получаются из низкокачественной стружки с корой и грязью, высушенной с несоблюдением технологии…
- Серые пеллеты получают из неокоренной древесины. На фото видно что пеллеты имеют включения коры. При уменьшении размера стружки включения могут быть и не видны, но пеллет будет иметь темноватый оттенок.
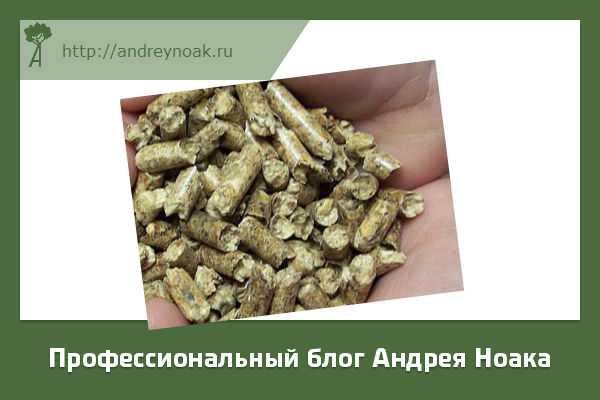
На фото серый пеллет.
- Светлый пеллет получают из качественной окоренной древесины. Светлый пеллет обладает большей теплоотдачей, меньше крошится и соответственно дороже стоит чем серые и черные гранулы.
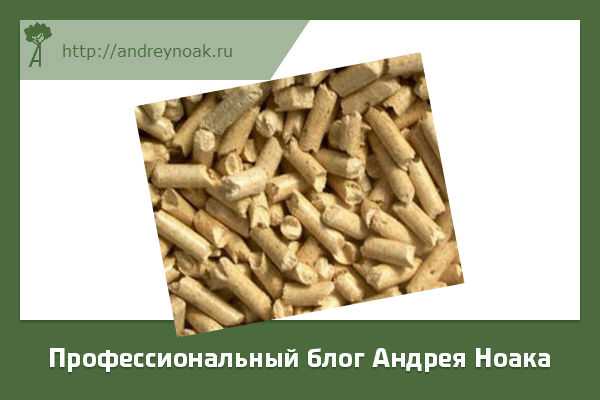
Самый высококачественный светлый пеллет.
Кроме цвета пеллет, от сырья зависит и качество склеивания пеллет. Дело в том что связующим веществом в процессе прессования пеллет является природный лигнин, который содержится в древесине. Но содержание лигнина в каждой породе разное, и соответственно чем больше лигнина содержится в древесине тем качественнее пеллет. Более подробно по этой ссылке.
Еще одним важным технологическим фактором при производстве гранул является такой параметр древесины как твердость. Дело в том что чем жестче древесина, тем больший износ режущего инструмента, матрицы и пуансона пресса.
Онлайн калькулятор расчета производства древесных гранул
Работа линии по производству пеллет
К сожалению просидев несколько часов в интернете мы не смогли найти информацию про работу оборудования на производстве пеллет. И вот получив опыт и знания, блог деревообработчика делится ценной и «вкусной» информацией со своими читателями, про работу «сердца» производства пеллетов — технологию прессования.
Итак, прессование осуществляется за счет продавливания через матрицу мелких опилок.
Опилки просыпаются на матрицу и затем вдавливаются в отверстия роликами катающимися по матрице. Количество роликов может быть разным, все зависит от производительности пресса. Выставляются ролики относительно матрицы с зазором. Принцип должен быть таким что первый ролик прокатывает опилки, второй придавливает на опилки, третий давит, четвертый пропихивает, пятый подчищает (то есть зазор каждого последующего ролика должен быть меньше к матрице чем предыдущий). Затем операция прессования роликами повторяется. Так как стружка для прессования используется подсушенная 6-15% (на каждый пресс, для каждой породы сырья подбирается индивидуально) и соответственно более жесткая чем сырая стружка, это способствует быстрому износу роликов и матрицы. Также на износ роликов пуансона и матрицы огромное влияние оказывает очень интересная технология запуска пресса, посмотреть как нужно правильно его запускать можно здесь.
При износе роликов пресса гранул уменьшаются углубления на роликах и соответственно стружка не может уже в достаточном объеме затягиваться между роликом и матрицей. Поэтому очень часто при данном износе начинает забивать пресс пеллет.
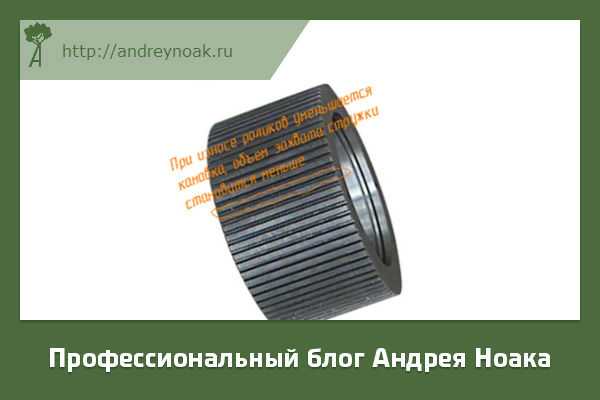
При износе роликов гранулятора, каемки становятся меньше и захват сырья на матрицу становится меньше…
При износе матрицы пресса пеллет стенки между ячейками матрицы становятся хрупкими, начинают крошится, ухудшается изготовление пеллет в качественных показателях.
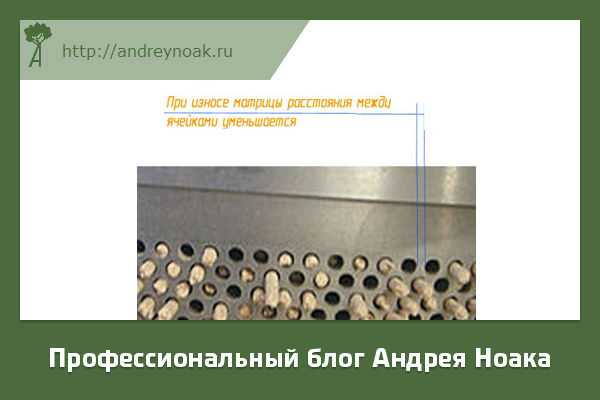
На фото показан износ отверстий матрицы пресса пеллет. Увеличиваются диаметры пеллет, Матрица начинает крошиться…
Тем не менее при установке новой матрицы и новых роликов для изготовления высококачественных гранул требуется какое то время для притирки рабочих механизмов, поэтому часто на новых механизмах можно не получить желаемое качество. Выше были перечислены естественные износы матрицы и роликов.
Также существует искусственный вариант выхода из строя матрицы и роликов — попадание твердых инородных частиц (камней, металла), на рабочих механизмах образуются впадины и прессование на данных участках не происходит. Качественное прессование это когда гранулы выдавливаются из всей поверхности матрицы, а не частями.
Выдавливание гранул только из некоторых частей матрицы говорит о том что пресс настроен неправильно, причин может быть множество это и выход из строя матрицы или роликов, колебания матрицы в посадочном месте, выход из строя подшипников на роликах и т.д…
Многие интересуются температурой прессования гранул — нормальной можно считать разогретый пресс от 60 до 100 градусов по Цельсию.
Упаковка пеллет
Пеллеты упаковываются в два вида тары:
- Биг бэг, эффективная фасовка для промышленных отопительных котлов.
- Фасованные пеллеты в полиэтиленовые мешки, хороша при использовании пеллет в домашних условиях.
О качественных показателях пеллет
Сегодня в России отсутствует единый ГОСТ на пеллеты, большинство ориентируются на DIN, очень хорошая статья с всеми DIN на пеллеты у нас тут.
Качество изготавливаемых гранул зависит от многих факторов, как технологических так и технических. К основным качественным показателям пеллет в процессе производства можно отнести:
- Длину готовых гранул
- Короткие пеллеты (низкого качества, возможно получение из за несоответствия влажности, износа рабочих механизмов, крупной стружки)
- Длинные пеллеты (нормальная длина пеллет 1,5-5 см)
- Технология пеллет особое внимание уделяет и прочности с целостностью гранул (окатыш не должен быть рыхлым, не должен быть порваным)
- Процент отсева при прессовании (данный параметр должен постоянно отслеживаться технологом, при большом проценте отсева значительно снижается производительность линии, увеличиваются затраты на производство пилетов)
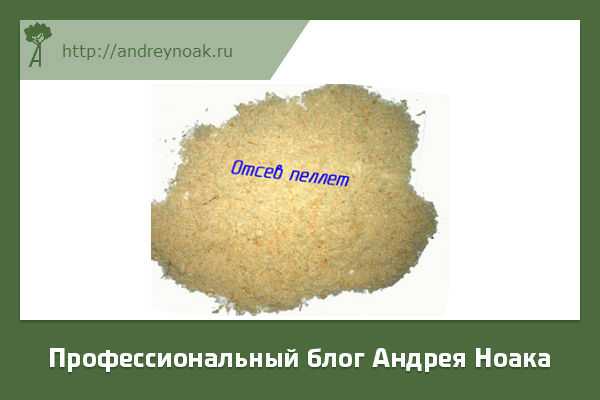
- Также последнее время особое внимание стало уделяться слому или срезу гранулы.
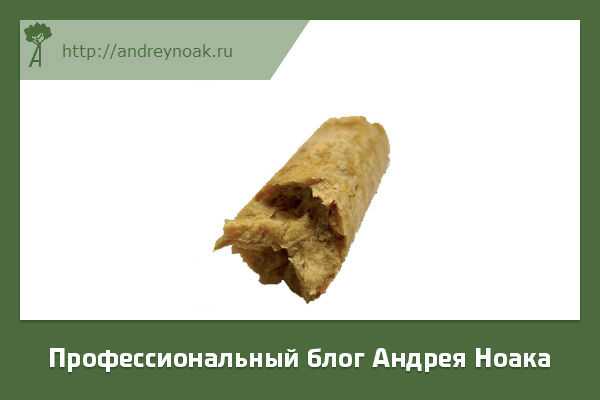
А вот что бывает если мы не используем обрезку гранул. При этом длина всех пеллет разная и образуется много отсева.
Все качественные показатели гранул между собой взаимосвязаны. И как правило при несоблюдении каких то технологических параметров (влажность, давление, фракционный состав) сразу снижаются все качественные показатели окатышей (так ласково их называют в Европе).
Качество пеллет зависит от:
- Правильно выбранной влажности сырья (окатыши со стружки повышенной влажности будут иметь больший объем чем гранулы со стружки пониженной и средней влажности при одинаковой массе)
- От фракционного состава сырья (чем крупнее стружка тем труднее ее спрессовать, при этом готовый окатыш с крупной стружкой может рассыпаться из за восстановления формы спрессованной стружки)
- От породы сырья (хвойные пеллеты получаются более качественные чем из пород лиственной древесины)
- От износа матрицы и роликов (при износе стружка не прессуется а накатывается на матрицу)
- От правильно настроенных зазоров между роликами и матрицей.
- От диаметра прессуемых пеллет (чем меньше диаметр пеллет тем лучше качество пеллет при одинаковых условиях прессования)
Книга в помощь
Очень часто производители оборудования пользуясь низкой квалификацией клиента продают просто штампованные линии не учитывая особенности сырья для пеллет, местности и погодных условий. В будущем чтобы исправить данные ошибки приходится вкладывать не малые средства, особенно если вы к примеру хотите продавать пеллет в Европу.
Более подробно про основные ошибки производителей оборудования можно узнать в моей новой книге «Типичные ошибки производителей оборудования при планировании производства пеллет». Более подробно о ней можно узнать на странице — МОИ КНИГИ.
Видео линии по производству пилетов:
Отличное тематическое видео о технологии производства пеллет:
Технология пеллет думаю теперь многим стала более понятна. В следующих статьях мы постараемся расширить наш с вами кругозор в этом направлении, поэтому подписывайтесь! Не стесняемся задаем вопросы, отвечу на все!
Удачи и до новых встреч!
andreynoak.ru
Завод по производству пеллет для малого бизнеса не требует больших инвестиций
Завод по производству пеллет требует мало инвестиций, но приносит большую прибыль. Ведь на пеллетном заводе производиться альтернативное топливо. Энергоресурсы всегда пользовались высоким спросом во все времена. Бизнес в отрасли энергоресурсов всегда имеет больше шансов на успех и процветание. Пеллеты сегодня все большую популярность набирают как альтернативное топливо. Его производят благодаря переработке отходов древесины и не только. Спрос на пеллеты растет с каждым днем. Оптовая стоимость 1т. пеллетного топлива начинается от 110$. Каждому заводу для производства или переработки нужно закупать сырье. Для производства пеллет в качестве сырья используют опилки из древесины, солому, шелуху из подсолнечника и т.п. Чтобы пеллетным заводом произвести одну тонну топливных гранул потребуется 7,4 кубометра опилок. Стоимость сырья составляет 5$ за куб (на условиях самовывоза). Получаем валовую прибыль: 110$ – (5$ * 7,4) = 73$ и это с одной только тонны альтернативного топлива. Даже при учете всех расходов (электроэнергия, зарплата, упаковка, транспорт) рентабельность бизнеса остается выше 100%. Показатель прибыльности завода по производству пеллет один из самых высоких по сравнению с другими видами бизнесов по переработке отходов. Рынок пеллетов охватывает все больше потребительских сфер. Ведь твердотопливные гранулы уже сегодня активно применяют: для отопления помещений, выработки электроэнергии на электростанциях, а так же начинают применять как альтернативу жидкому топливу для грузовых автомобилей с помощью газогенераторов. Бизнес идея по производству пеллетных гранул – это целая энергетическая промышленность, которую можно реализовать при минимальных инвестициях.
На заводе должны производиться качественные пеллеты
Чтобы запустить заводское производство пеллет, следует изучить технологию. Пеллеты были изобретены еще в середине прошлого века. Придумал их Рудольф Гуннерман. Они искал решение для сокращения расходов на вывозе отходов из своей лесопилки. И решил опилки прессовать прямо на заводе перед вывозом, чтобы в несколько раз уменьшить объем отходов. Но оказалось, что прессованные опилки и стружка горят значительно лучше и эффективнее обычной древесины. Благодаря высоким показателям горючести теплотворность пеллет выше в 2.5 раза. Чем больше углерода в древесном топливе, тем выше его теплотворность. Дело в том, что обычное необработанное дерево кроме горючего углерода в молекулах целлюлозы содержит еще значительное количество водорода и кислорода. А при измельчении дерева молекулы целлюлозы разрушаются и атомы водорода, кислорода из нее уходят в виде летучих газов. Еще существенным преимуществом пеллетных гранул от дерева является сгораемость материала. Дерево при сгорании теряет 85% массы в виде летучих газов, остальные 15% составляет зола. А при сгорании пеллет золы остается всего 0,75-1,5% (почти в 20 раз меньше) в зависимости от сырья из которого они произведены. Так же важно отметить, что топливные гранулы в 2 раза меньше содержат влаги в отличие от дерева. В процессе производства под высоким давлением пеллеты прогреваются до 110 градусов Цельсия, что позволяет вдвое сократить содержание влаги. Кроме того за счет прессования топливные гранулы обладают более высокой плотностью чем дерево. Проверить данный факт очень легко. Дерево, как известно в воде не тонет, плавая на поверхности, а пеллетные гранулы, произведенные из древесных опилок, камнем идут на дно. Это так же объясняет, почему из меньшего объема гранулированного топлива получается значительно больше тепла при сгорании, чем у дерева. Фактически пеллеты это горючее топливо, которое набирает большую популярность во время энергетического кризиса. Оно обладает своими особенностями такими как: высокая безопасность топлива, низкая стоимость и другие преимущества.
Технология производства пеллет для малого завода
Бизнес по производству пеллет –
это завод по переработке отходов.
Заниматься переработкой отходов – актуально, выгодно и гуманно.
Особенно выгодно если перерабатывать отходы в топливо безопасное для
окружающей среды. На заводе можно производить пеллеты из различного
вида сырья: древесных опилок, стружки, коры, соломы, шелухи
подсолнечника, сухих стеблей кукурузы и т.п. Конечно, пеллетные гранулы
могут отличаться по своим характерным свойствам в зависимости от сырья,
из которого их производят. Главный показатель, влияющий на стоимость
древесных гранул – процент зольности. Чем выше процентное содержание
золы, тем ниже стоимость гранулированной древесины. Технология
производства пеллет проста и понятна. Сырье при необходимости следует
измельчить до размера мелких опилок (тирсы) и если
нужно предварительно
подсушить (рекомендуемая влажность сырья до 20%).
После чего опилки
подаются в роликовый или шнековый пресс-гранулятор где подобно
мясорубки выдавливаются через специальную решетчатую матрицу готовые
цилиндрические пеллеты. Каждое дерево в своем составе содержит клеящее
вещество «лигнин». Благодаря лигнину из опилок формируются цельные
гранулы цилиндрической формы. Опилки в прессе-грануляторе нагреваются и
выделяют лигнин, который под воздействием температуры превращается в
натуральный природный клей. Древесная смола сама по себе горит долго и
ровно.
Заводу нужно поставить прессовочное оборудование
Оборудование для завода по производству пеллет вполне доступно как для малого, так и для домашнего бизнеса. Пресса-грануляторы могут быть роликового или шнекового типа. Стоимость прессов напрямую зависит от производительности. Например, пресса производительностью в 250 кг/час уже доступны по цене 6200$ с мощностью электродвигателя 15 кВт., для 380В. Хотя существуют и более компромиссные предложения с меньшей производительностью и ценой пресса. Для производства пеллет из соломы заводу потребуется дополнительное оборудование – измельчитель. Можно использовать ДКУ, который обойдется по цене 1000$ с производительностью 100кг/час для фракций размером 3мм. Важно отметить, что при постоянной работе пресса-гранулятора , через 2,5-3 месяца потребуется замена деталей узлов высокого давления. В управлении производством правильно контролируйте постоянные расходы средств на решетчатую матрицу, ролики или шнек (в зависимости от типа пресса) – основные рабочие части гранулятора. При производстве пеллетов только из соломы или другого мягкого сырья рабочие детали пресса могут прослужить вдвое больше. А так же производительность будет несколько выше при одних и тех же нагрузках, что благотворно отразится на расходах электроэнергии.
Потребность в пеллетах все больше испытывают альтернативные отопительные системы
У каждого производственного или перерабатывающего завода стоит главный вопрос о сбыте продукции. Отопление помещений пеллетами на специальных котлах – сегодня наиболее популярное применение для данной продукции. Но существуют и другие рынки сбыта. Например, в области наполнителей для туалетов домашних животных. В Европе уже давно используют, а у нас только набирают популярность пеллетные (гранульные) котлы с очень высоким КПД (85-85%). Данный вид твердотопливных котлов отличается своей повышенной продолжительностью работы без участия человека на протяжении 7 суток и более. Такая возможность достигается благодаря сыпучести гранул, с помощью которой осуществляется заправка котла твердым топливом через программный контроллер управляющим шнеком подачи. Весь процесс дозаправки котла происходит автоматически. Уровень автоматизации котла позволяет самостоятельно подавать новую порцию гранулированной древесины из бункера для поддержания заданной температуры. Специальный электрический тэн и вентилятор могут взять на себя автоматический розжиг топливных гранул. Так же котлы оборудованы специальной гранульной горелкой, которая позволяет максимально эффективно использовать пеллетное твердое топливо. Пеллетные котлы не требуют особого обслуживания. Чистка золы осуществляется 1 раз в месяц. Мощность котлов начинается от бытовых потребностей 15-500кВт и может достигать до 2МВт для промышленных целей. Срок службы котлов один из самых высоких – более 20 лет. На картинге изображен гранульный котел австрийской фирмы OkoFen. Описание устройства котла:
- Камера рециркуляционного горения.
- Микропроцессорное управление.
- Самоочищающаяся система.
- Пульт управления регулировки температуры.
- Камера из высококачественной стали.
- Гранульная горелка.
- Дополнительная система очистки.
- Электроподжиг топливных гранул.
- Место для установки горелки с обратной стороны.
- Система пожарной безопасности.
- Бокс для пепла.
- Автоматическая подача гранул.
- Климатконтроль.
- Контроллер давления.
- Воздухозаборник.
Пеллетные котлы являются серьезной альтернативой газовым котлам. Хотя сама гранулированная древесина прекрасно себя зарекомендовали как высокоэффективное топливо в обычных твердотопливных котлах и даже простых печках как лучшая альтернатива дровам. Ниже приведены еще примеры потребления эффективного пеллетного топлива.
Пеллетами можно заправлять автомобили
Cбыт пелет заводского малого производства будет существенно расширен. Уже сегодня ездят автомобили на полетном топливе. Всем известно, что в середине прошлого века грузовые автомобили работали на древесном топливе. Двигатель внутреннего загорания тот же самый что и для традиционного топлива. Фактически в место бензина использовался горючий газ, получаемый из газогенератора путем пиролизации древесины. Газогенератор – это устройство для преобразования в газообразную форму твердых горючих материалов. Данное физическое явления называется пиролиз – распад тяжелых молекул на легкие под воздействием повышения температуры и недостатка кислорода. На пример обычный автомобиль «Газель» оборудован газогенератором расходует 1кг. древесины на 1км. То есть на 100км необходимо было возить в кузове 100кг древесины. Так использовалось много полезного пространства в кузове автомобиля на объем дров и габаритов газогенераторной установки. Дозаправка газогенератора древами осуществлялась вручную через каждые 50км. Разгон автомобиля необходимо было производить плавно, предоставляя газогенератору время для перехода на повышенный режим мощности. Благодаря пеллетам все недостатки автомобилей на газогенераторных установках практически устраняются. Их сыпучесть позволила автоматически заправлять газогенератор, так как в общей массе они представляют из себя псевдожидкость. Габариты и масса газогенераторной установки стали значительно меньше. Электронная микропроцессорная система отслеживает ускорение автомобиля и автоматически подключает традиционное топливо в момент резкого изменения нагрузок на двигатель акселератором. Приемистость автомобиля полностью сохраняется. К тому же пеллеты благодаря большей плотности и теплотворности активнее выделяют газ и реже нуждаются в паузах для перехода на другую мощность работы генератора. Тем более на грузовых автомобилях. Все преимущества гранулированного топлива в отношении к древесине пригодились для использования их как топливо для грузовых автомобилей с газогенераторными установками. Плотность и теплотворность топливных гранул требуют значительно меньше полезного пространства в кузове. Пеллеты в 3 раза снизили расход потребления твердого топлива до 0,3кг на 1км. Даже при краткосрочном использовании бензина в моменты резкого ускорения автомобиля, уже расход меньше в 2 раза в отношении к традиционным видам горючего. Если ездить в экономичном режиме, можно вообще отказаться от использования бензина. Тогда стоимость 1км составит 0,04$. 1кг пеллетов = 0,11$ / 3 (расход на 1км = 0,3кг) = 0,04$/км. Еще важно отметить, что при сгорании газа созданного путем перолиза древесных гранул не выделяются вредные, токсичные вещества. Это экологически-чистый вид топлива.
Пеллеты использую как топливо для электростанций
Рынок потребления пеллет растет с каждым днем. К 2020 году Европейский Союз планирует на 20% снизить количество вредных выбросов в атмосферу. Для этого планируется уже в 2015 году увеличить объемы использования твердого БИО-топлива до 50 %. Основными потребителями станут электростанции на пеллетах. На сегодняшний день это самые дешевые «зеленые электростанции» по сравнению даже солнечными и ветровыми станциями. Пеллеты обладают высокими энергетическими показателями. Все крупные электростанции Европы переходят на гранулированное древесное топливо. Только начинают появляться в продаже мобильные электростанции на гранулированном топливе. Все больше устанавливается котлов, работающих на древесных гранулах. С подорожанием нефти и газа будут выпускать все больше газогенераторных установок для грузовых автомобилей и сельхозтехники. Сегодня мы находимся в самом начале развития использования нового вида топлива. Потребности в нем будут расти постоянно. Важно отметить, что у малого или домашнего бизнеса уже сейчас имеется возможность начать производить топливо нового поколения при небольших инвестициях. Уже сейчас нужно быть готовым к активному росту рынка.
businessideas.com.ua
хорошая технология всегда в цене
Здравствуйте уважаемые читатели и подписчики блога, на связи Андрей Ноак! Сегодня я расскажу вам про производство пеллетов из опилок, с какими трудностями вы можете столкнуться и как лучше организовать технологию. Идея для сегодняшней статьи взята с моей командировки в качестве консультанта на производство гранул, находящееся недалеко от г. Казани. Я буду рассказывать как играя с технологией можно значительно оптимизировать изготовление пеллет.
Информация которая дана тут на самом деле очень ценная, ее даже не все в свой бизнес план включают, а надо бы знать такие вещи и предусматривать соответствующие площади.
Сырье
Огромные кучи опилок в нашей необъятной стране впечатляют не только наших соседей из Европы но и местных жителей, которые живут в этих районах. В последние годы правда ситуация сдвинулась в лучшую сторону, строятся новые заводы по производству древесных плит из стружки и щепы, а особой популярностью обладают производства для изготовления древесных гранул.
Рентабельность такого предприятия может достигать 40%, штат работников в одну смену 2 человека и никаких отходов! При этом еще и древесина для производства бесплатная, так как бесплатных отходов у нас в стране хоть отбавляй!
Перед планированием производства нужно учесть ряд факторов, один из них сырье, его размеры, влажность, наличие коры и вообще имеющиеся виды.
Так, а теперь обо всем по порядку.
Крупные древесные отходы в опилках
Опилки опилкам рознь, поэтому перед приобретением оборудования нужно обратить внимание вот на что — наличие крупных отходов и стружки в общей массе древесного сырья.
Многие производители ставят на этапе подачи сырья со склада сито для сортировки стружки, не учитывая реалии производства. При этом клиенту нужно заплатить за это сито не мало средств. Другие не ставят сито, хотя надо бы. Сейчас я расскажу когда его надо и какими параметрами оно должно обладать.
Сито необходимо только на то производство, где действительно имеются крупные тяжелые кусковые отходы, а это к примеру куски горбыля отлетника, различные так называемые лещи и эти кусковые отходы могут привести к возгоранию в сушильном комплексе, а возможности вручную убрать их все просто не предоставляется.
Некоторые производители оборудования ставят сито на сортировку, внимание … фуговальной стружки. Для тех кто ее не знает,это стружка которая завитая. Тут нужно сразу ставить в задание заводу производителю, чтобы такая стружка без проблем у вас сушилась и перерабатывалась. А выкидывать эту стружку в отходы и
ли дополнительно ее дробить, неся большие затраты на это – неправильный подход. Фуговальная щепка на большинстве предприятий сушится и дробится без проблем, не нуждаясь в дополнительном измельчении.
Еще сито сортировки сырья обязательно должно регулироваться на различную фракцию, которую вы подберете со временем исходя из своего опыта и рекомендаций производителя. Дело в том, что некоторые производители поставляют обычные стандартные сита, которые не регулируются.
Отходы от сита:
- Это минеральные примеси, такие как камни, металл. Их утилизация это свалка;
- Зимой это куски льда и снега которые снижают производительность сушильного комплекса. Раскрою небольшой секрет, чтобы не выкидывать снежные камни с стружкой или просто стружку смерзшуюся в камень на свалку, мы откладывали ее в сторону и потом после растаивания снега у нас появлялось дополнительное масса древесины для гранул;
- Куски горбыля, бакулки, ветви, лещи — если такие имеются, то в технологии производства гранул нужно рассмотреть вариант их дробления в опилки, это можно сделать на барабанной или дисковой дробилке;
Следующий этап это виды сырья
На большинство пеллетных производств древесные отходы поступают с разных лесопильных предприятий, или с одного предприятия, но с разных деревообрабатывающих линий. Это может быть, к примеру, столярный цех, лесопильная рама без окорки и сортировки и третье это линия лесопиления с подсортировкой леса и его окоркой или какие то другие варианты, главное это нам нужно сейчас с вами уловить суть.
Технология изготовления гранул предполагает рассортировку стружки по влажности и качеству. Сырье с столярного цеха нам не нужно сушить, ведь тут уже мы имеем нужные нам 10-12%, поэтому его складируем в бункер после сушильного барабана. Так мы сможем сэкономить на его прохождении через барабан. Оно не имеет в своем наличии минеральных примесей, коры. Из него выйдет отличные светлые гранулы.
Отходы от лесопильной рамы, где лес не окаривается и не сортируется, имеет в своем составе около 25% коры. Из него мы получим только темные гранулы, складируем его отдельно от других древесных отходов перед сушильным комплексом на площадке или если имеется ангар, то в нем. После того как мы накапливаем к примеру таких опилок на неделю работы, мы перестраиваемся на темный пеллет и работаем.
Сырье от лесопильной линии с окоркой, такая стружка содержит минимум коры и из нее получится качественный белый пеллет. Копим его на какой то срок работы и запускаем цех работать только на нем.
Технологическая гибкость оборудования для пеллетов
У нас выходит три вида сырья. Сразу хочу сказать что для сырья со столярного цеха вам придется делать отдельный бункер который будет запаралелен с бункером после сушилки. Этот бункер должен иметь такой объем, чтобы можно было спокойно там складировать древесной массы на неделю работы. При переходе на сухую стружку, у вас отменяется этап сушки (а это колоссальная экономия энергии) и вам не нужен в штате второй оператор, работающий на сушильном барабане. Поэтому тут штат нужно будет формировать с этим учетом.
Кстати вы можете с легкостью мешать стружку для получения большей выгоды для себя. К примеру вы имеете сухое сырье с столярного цеха, и имеется некоторый запас опилок с корой. Запускаете производство на опилках со столярки и небольшими порциями подмешиваете опилки с корой. Готовый пеллет остается светлым, незначительно меняя свой оттенок на более темный. А вы производите больший объем более дорогих светлых древесных окатышей.
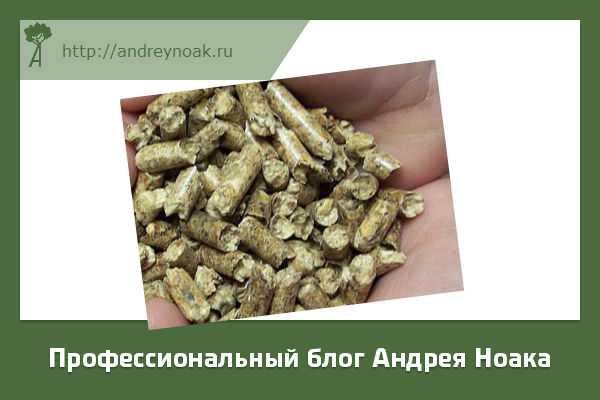
На фото серый пеллет. Его принимают за светлые гранулы и он продается по стоимости светлых окатышей…
Бункер опилок после сушилки также должен иметь достаточный объем, я думаю хотя бы на несколько суток работы главного конвейера. Это позволит к примеру при небольших поломках, на несколько часов, главного конвейера не останавливать сушильный комплекс и наоборот.
Кроме этого к примеру бывает очень часто что сушилка и пресс имеют разную производительность. Большой бункер сырья позволит не вызывать каждую смену два оператора и чтобы один из них работал в полсилы. А вызвать одного оператора чтобы он насушил за смену на несколько смен работы гранулятора и затем отдыхал. Так появляется большая технологическая гибкость оборудования.
Переход с одного вида сырья на другое
Переход со светлого на темный пеллет и наоборот, осуществляется при наличии сырья на несколько дней работы.
Для перехода с темного пеллета на светлый, вырабатываем все опилки с корой в бункере перед сушилкой. Опустошаем бункер после сушилки (израбатываем всю стружку). Опустошаем охладитель гранул и фасовочный бункер.
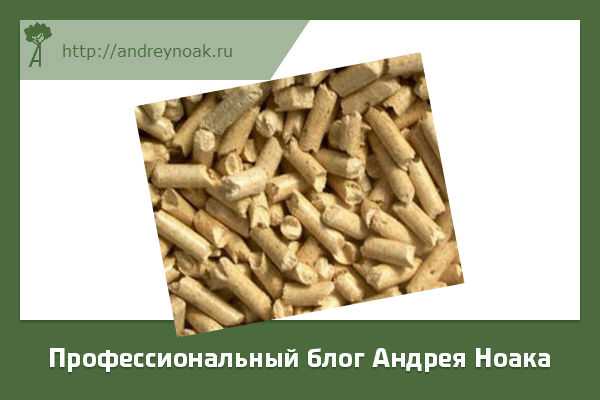
Самый высококачественный светлый пеллет.
Начинаем сушку светлых опилок (которые без коры) и запускаем главный конвейер. После запуска пресса у нас будет первое время выходить темный пеллет, так как на линии остались еще темные опилки. Мы темные гранулы маркируем как темные. Через некоторое время будут гранулы белее и затем пойдет светлая гранула. Как пошли достаточно белые окатыши упаковываем и маркируем их как светлые.
При переходе с светлого на темный, все выполняется в той же последовательности.
Мои услуги и книги
Как я уже говорил могу помочь с выводом производства на большую производительность, с правильной модернизацией оборудования, с подбором б/у линиии или станка. Также ко мне часто обращаются люди просто за советом. Сегодняшняя информация еще более подробно изложена в моей новой книге «ТИПИЧНЫЕ ОШИБКИ ПРОИЗВОДИТЕЛЕЙ ОБОРУДОВАНИЯ ПРИ ПРОИЗВОДСТВЕ ПЕЛЛЕТ». Более подробно о ней в разделе «МОИ КНИГИ».
Видео по теме
Пока пока, с вами был Андрей Ноак!
andreynoak.ru
пеллеты и брикеты из отходов, биоэтанол и биодизель
Дата публикации: 23 декабря 2013
Древесные топливные гранулы – пеллеты
Завод по производству биотоплива – пелетт, как правило, располагается вблизи источников сырья, например, около деревообрабатывающих предприятий крупного масштаба.
Для производства гранул, используемых в качестве топлива при отоплении жилых помещений, применяется древесина, процент коры в которой сведен к минимуму (около 0,5%), а зольность – очень незначительная. Что касается именно промышленных пеллет, то технология их изготовления позволяет использование древесины с содержанием коры до 10%.
Дробление исходного материала крупными кусками
Первоначальный этап производства пеллет подразумевает дробление исходного материала, которое осуществляется в специально оборудованных дробилках. Габариты древесных кусочков, которые выходят из дробилок, не должны быть более 25x25x2 мм, ведь именно такие размеры наиболее оптимальны для полной сушки материала, подлежащего дальнейшему дроблению в мелкой дробилке.
Процесс сушки
Материал, влажность которого повышена, плохо поддается прессованию, поэтому те гранулы, которые будут из него сделаны, плохо горят. Именно по этой причине сушка является одним из важнейших этапов при производстве пеллет, она может существенно сократить влажность древесного материала (9-12%). Оптимальной считается влажность щепок или опилок, равная 10%, — такое сырье самое качественное.
Сушилки, в которые подают сырье, могут быть как ленточные, так и барабанные: чтобы выбрать ту или иную модификацию, следует отталкиваться от используемого сырья (опилки либо щепа), а также от требований к конечному продукту.
Сушку считают одним из самых энергозатратных процессов в изготовлении пеллет: чтобы просушить тонну материала, нужно применить теплоту, получаемую от сжигания куба дров высокой плотности. Сжигать доски или бревна целиком выходит очень затратно, именно по этой причине изготовителями используются опилки или кора при производстве пеллет.
Дробление
Частицы материала, которые готовят для последующего прессования, не должны превышать размер 4 мм. Для этого применяют оборудование для биотоплива — специализированные дробилки, способные измельчить сырье до нужного размера. Самыми лучшими дробилками, способными эффективно измельчить опилки или щепки, являются молотковые мельницы.
Подготовка воды
Может случиться так, что высушенное сырье оказывается более сухим, чем следует, например, при оптимальной влажности в 10%, снижение показателя до 1-8 % может негативно сказаться на склеивании сырья при прессовании. Чтобы повысить влажность до необходимой отметки, материал погружают в специальную емкость, в которой он обрабатывается водой и паром. Использование горячего пара необходимо в процессе опрессовывания древесины и при распаривании залежавшегося сырья. Что касается мягких пород древесины, то в данном случае будет достаточно добавить в емкость для смешивания жидкость.
Процесс прессования
При прессовании первоначальный материал преобразуется в маленькие цилиндры, диаметр которых не превышает 5-25 мм. При их производстве специально обработанный материал проходит свой технологический цикл, включающий формовку на специальных прессах. Измельченное древесное сырье прессуется и сжимается, а при возрастании температуры оно выделяет особое вещество – легнин, склеивающее малейшие частички в специальные гранулы.
Охлаждение
При прессовании гранулы могут нагреваться до температуры 80-90 градусов, что требует дальнейшего охлаждения и сушки, после чего полностью готовое биотопливо — пеллеты подлежат упаковке.
Расфасовка
Зачастую биотопливо — пеллеты хранят в оборудованных бункерах, но для поддержания высокого качества их желательно расфасовывать в большие мешки. Для применения пеллет при отоплении жилых помещений биотопливо, как правило, поставляют в мешках, фасованных по 20 кг.
Древесные брикеты
В процессе изготовления брикетов, материал сжимают под высоким давлением, при этом температура повышается от трения, что приводит к выделению лигнина и склеиванию частей брикета. Если биотопливо выполнено не из древесного материала, то в нем могут присутствовать натуральные добавки (около 2%). Во время производства такой продукции нужно следить за влажностью, которая является важнейшим параметром, способствующим плотности брикета. При повышении уровня влажности до 14 % такое биотопливо, как брикет, может расклеиться и разделиться на множество кусков, что нежелательно
Биотопливо в виде брикетов удобно хранить и транспортировать, ведь готовый брикет составляет десятую часть объема всего материала, потраченного на его изготовление. Для того, чтобы производить древесные брикеты, используются различные прессы – шнековые, поршневые, а материалом служат опилки и отходы в виде стружек. Перед тем, как начать процесс прессования, сырье измельчается и высушивается до состояния влажности не более 14%.
Работа поршневого пресса происходит циклическим образом: каждый ход поршня проталкивает некоторое количество сырья через сопло конической формы, что приводит к образованию на самих брикетах слоев. Маховик, который используется в приводе, выравнивает нагрузку на двигатель. Поршень в процессе работы изнашивается медленно, ведь перемещение между прессуемым сырьем и поршнем незначительно, а вот сопло изнашивается довольно скоро. Такие прессы стоят относительно недорого и очень распространены.
Гораздо легче предыдущего считается установка – шнековый пресс, из-за отсутствия в его конструкции поршней и маховиков. Брикеты разрезаются на нужные по размеру куски, материал выходит непрерывным конвейером. Такие прессы производят мало шума, ввиду отсутствия ударной нагрузки, но потребляют много энергии, а шнек быстро изнашивается.
Изготовление древесного угля
Древесный уголь изготавливается несколькими способами, при этом выбор конкретной технологии подразумевает и выбор материала, и свойства конечного продукта.
В основном, для изготовления древесного угля используются особые печи для выжигания (ретортный тип).
Сжигание сырья – древесины, должно происходить без присутствия кислорода, что означает «пиролиз». Технология производства имеет свои этапы и осуществляется следующим образом: древесина укладывается в реторты, устанавливаемые в сушильной камере или камере безкислородного сжигания. В топочном отсеке разжигают дрова, а когда температура достигает необходимой отметки, древесина начинает сжигаться без поступления кислорода.
Газы, выделяемые при этом процессе, не попадают в атмосферу, а расходуются на поддержание горения. Как только установка вошла в рабочее состояние, дрова начинают расходоваться минимально, а требуемая энергия тепла образуется из газов. В связи с этим, для более эффективной работы, технология изготовления угля предусматривает непрерывный процесс, например, пару смен.
Как только процессы пиролиза завершаются, реторта с конечным продуктом выкладывается на решетку, где она остывает, а на ее место отправляется новая, только что из сушилки. Все реторты проходят несколько этапов, среди которых загрузка, процесс сушки, сжигание без кислорода, охлаждение путем остывания и выгрузка.
Оборудование не вентилируется, так как оно не оснащено газовыми нагнетателями, что сводит энергозатраты к минимуму, нужно только электричество для освещения в вечернее и ночное время. Если применяются большие печи, то дополнительные энергозатраты могут быть связаны с колкой дров и использованием подъемного устройства.
Необходимо уточнить, что на сегодняшний день используется также технология изготовления древесного угля из брикетов, а не из древесины. Тогда уголь выходит более высокого качества, а его производство не предусматривает отходов, ведь даже мелкие щепки подойдут для сжигания.
Биоэтанол
Сырье – древесина или солома, которое поступает для производства биоэтанола, проходит этап отбора и приема: его взвешивают, очищают от добавок, а затем отправляют на измельчение. Чтобы измельчить материал, его поставляют на дробилки (валковые или молотковые), которые способны обеспечить требуемые размеры, что сказывается на качестве последующей переработки материала.
Есть несколько вариантов производства биоэтанола – сухой и влажный, различие этих способов состоит, в основном, в образовании клейковины и крахмалов, образуемых при втором варианте.
При сухом способе, биоэтанол получают путем смешивания муки и воды, при этом образуемая смесь осахаривается, а крахмал, находящийся в суспензии, под влиянием высоких температур и ферментации преобразуется в сахара и сбраживается.
Второй способ производства – это брожение осахаренного материала, которое проходит в специальных чанах, предназначенных для сусла. В него добавляют дрожжи, которые перерабатывают образуемые сахара в спирт, точнее, в брагу (% спирта в такой жидкости – около 8%). Чтобы получить необходимую концентрацию спирта, бражка очищается на этапе дистилляции, таким образом, получают чистый спирт 96%. Колонны с молекулярными ситами способны обезводить спирт до состояния биоэтанола (крепостью 99,8%). Стадия абсолютирования является конечной, после нее биоэтанол помещается в хранилище спирта, а далее производится его отгрузка любым видом транспорта.
Во время этапа дистилляции образуется главный отход производства – это барда послеспиртовая, пригодная для изготовления кормовых дрожжей и биогаза. Высушенная барда применяется также при кормлении животных. Дрожжи для кормления скота – это очень ценная добавка из белка, которую используют при изготовлении комбикормов и смесей, подходящих для кормления практически всех животных, а также птиц и рыбы.
Одним словом – технология получения всех продуктов переработки практически безотходна.
Биодизель
Чтобы получить биотопливо – биодизель, используется следующее сырье: рапс, соя, пальмовое, кокосовое и касторовое масла. Технология такова — в очищенное масло добавляется метиловый спирт и раствор щелочи, служащей как катализатор.
Полученная смесь подвергается нагреванию до 50 °С, после чего происходит ее расслоение на две составляющие – легкую и тяжелую фракции. Легкая фракция – это метиловый спирт, а именно – биодизель, а тяжелая – глицерин.
Исследования показали, что такое биотопливо по своему составу схоже с дизельным топливом. Применяемая технология позволяет следующее — переработав 1 тонну семян рапса можно получить до 300 кг рапсового масла, а впоследствии – 270 кг биодизеля. Выход глицерина при этом составляет около 10%.
Применение биодизеля возможно как в чистом виде, так и в виде добавок к солярке, размер которых варьируется от 5 до 35% от общего объема топлива. Данное биотопливо отличается от минерального топлива хорошими смазывающими свойствами и продлевает срок эксплуатации двигателей, так как способствует удалению отложений нефтепродуктов в системе мотора.
О.Баратова
altenergiya.ru
виды сырья, технологический процесс :: BusinessMan.ru
Основной предпосылкой для поиска новых видов энергоносителей является неизбежное скорое истощение традиционных природных ресурсов – нефти и газа.
Разработкой альтернативных видов топлива человечество озабочено уже не один десяток лет. Одним из вариантов современного высокотехнологичного вида энергоносителей можно по праву считать пеллеты (паллеты) или евродрова.
Описание горючих брикетов
Гранулированное топливо представляет собой отходы лесной промышленности, спрессованные в виде мелких элементов цилиндрической формы. Сырьем для производства пеллет могут выступать многочисленные древесные отходы в виде опилок, стружки, коры, некондиционной древесины. Евродрова представляют собой чистый в экологическом отношении вид топлива, отличающийся высокой степенью теплоотдачи с пониженной зольностью.
Отличной альтернативой древесному сырью могут также служить отхожие продукты переработки сельскохозяйственных культур. К ним относится солома, лузга подсолнечника, риса, кукурузы и шелуха различных зерновых культур. Особенно актуальным будет такое сырье в аграрных районах с редкими лесными массивами.
Где производят пеллеты (паллеты)?
Для запуска предприятия по переработке отходов требуются значительные финансовые вложения. Небольшим хозяйствам может быть по силам покупка мини-грануляторов. Такие установки работают на электрическом или дизельном двигателе. Компактные размеры позволяют свободно перевозить их для установки в места непосредственного сбора отходов (лесопилки, деревообрабатывающие и мебельные цеха).
Оборудование для производства паллет из опилок промышленным способом устанавливается на небольших заводах полного цикла с набором специального оборудования и просторными складскими помещениями. Подрядная организация сама осуществляет доставку, монтаж, наладку и запуск линии.
Оптимальный вариант покупки предполагает, что оборудование для производства паллет должно быть сдано поставщиком полностью готовым к работе. Для уверенности в дальнейшей стабильности рабочего процесса желательно подписать с подрядчиком договор о сервисном обслуживании.
Полная окупаемость затрат на оборудование для производства паллет наступает примерно через год. Рентабельность предприятия составляет в среднем 110%. Это отличный результат, на который можно уверенно ориентироваться в ближайшие пятьдесят лет.
Основные этапы производства
С увеличением спроса на альтернативные виды топлива неизбежно возрастает интерес к технологическому процессу изготовления евробрикетов. Линия для производства паллет включает в себя несколько основных циклов.
На первом этапе происходит начальное дробление исходных материалов в специальных дробилках. Подготовленное и взвешенное сырье измельчается до частиц объемом не более одного кубического сантиметра каждая.
Полученные полуфабрикаты помещаются в сушилку барабанного или ленточного типа. Цель процесса – снижение влажности до уровня 8-12%. Затем происходит повторное дробление до более мелкого состояния частиц – муки. Для этого используют молотковые мельницы.
Высушенные компоненты помещаются в смесительные емкости, где смачиваются водой до определенной степени кондиционирования. Этот этап является очень важным звеном в общей цепочке производственного процесса, потому что от показателя влажности зависит степень дальнейшего склеивания сырья.
Пресс – это главный станок для производства паллетов. Увлажненная мука попадает под прессующие вальцы, которые продавливают ее через круглые отверстия матрицы при высокой температуре. Выходящие из отверстий пеллеты обрезаются специальным статичным ножом на маленькие брусочки.
Горячие гранулы незамедлительно отправляются через рукав кожуха пресса в охладительную колонку. Здесь происходит охлаждение пеллет и отсеивание излишков муки.
На последней стадии процесса происходит просеивание и упаковывание готовых гранул.
Рынок сбыта пеллет
Изготовление гранулированного топлива является экономически выгодным для предприятий-производителей. Постоянный поиск потребителем различных способов удешевления отопления гарантирует стабильный спрос на пеллеты (паллеты). Поскольку источники сырья для производства гранул напрямую зависят от жизнедеятельности человека, то их можно считать неиссякаемыми.
Сегодня многие домовладельцы отапливают свое жилье при помощи специальных котлов, работающих на экологическом топливе. Все более учащаются случаи установки газово-пеллетных установок в котельных небольших промышленных предприятий, учреждений, больницах, школах и детских садах.
Есть еще одна важная категория потребителей натуральных пеллет – владельцы домашних кошек. Они активно используют гранулированные изделия в качестве сменных наполнителей для кошачьих биотуалетов.
businessman.ru
изготовление и расход пеллет из древесных опилок
Пеллеты торфяные, как и другие варианты такого вида топлива, пользуются заслуженной популярностью, благодаря многим своим достоинствам. Например, их теплотворная способность может сравниться с угольной, а дерево проигрывает этим гранулам во много раз. При сгорании пеллет выбросы вредных веществ в атмосферу минимальны, а выделение тепла велико и происходит равномерно.
Видео: что такое пеллеты
Визуально пеллеты или топливные гранулы представляют собой цилиндрические спрессованные отходы деревообработки или другие вещества. Их можно изготавливать из
- куриного помета;
- торфа;
- соломы;
- отходов крупяного производства;
- лузги подсолнечника.
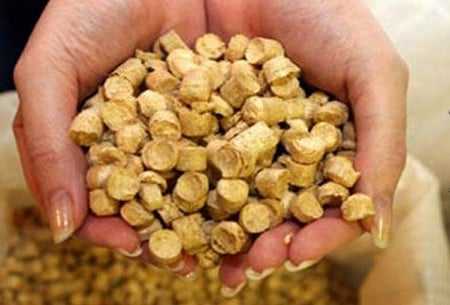
Древесные пеллеты
Достоинства и недостатки топливных гранул
Преимущества пеллет таковы:
- низкий риск самовоспламенения;
- не содержат пыли и спор, то есть безвредны для людей, страдающих от аллергии;
- экологическая чистота, ведь при сжигании гранулы пеллеты выделяют до 3 процентов золы;
- высокая производительность тепла;
- большая плотность, облегчающая транспортировку гранул.
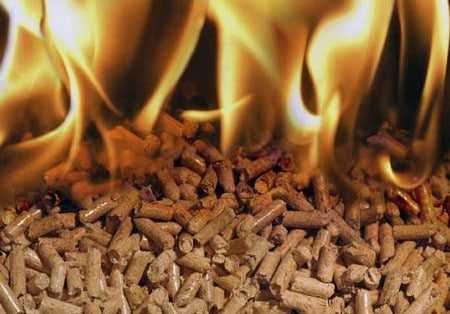
Небольшое количество гранул пеллет дает большой жар
Топливные гранулы могут иметь такие минусы:
- возможность распыления в воздух вредных веществ, если таковые имелись в среде, где было собрано сырье;
- высокая стоимость при покупке малого количества топлива.
Где можно использовать такое топливо
Топливные пеллеты широко распространены в странах Европы, где их используют как для частных домов, так и для отопления целых районов. Кстати, даже если в уголь просто добавляют древесные гранулы, это уже способствует сокращению вредных выбросов в атмосферу.
Использовать пеллеты можно:
- в жилых домах частного владения в каминах или котлах;
- в котельных жилищно-коммунального хозяйства;
- в системах комбинированного производства электроэнергии и тепла;
- в кошачьих туалетах в качестве наполнителей
- в аварийных ситуациях при необходимости локализовать и удалить жидкие продукты.
Основные этапы производства пеллет
Топливные гранулы производятся обычно промышленными масштабами, но ничто не мешает изготавливать пеллеты своими руками. Для этого стоит понимать, в чем заключается процесс их изготовления.
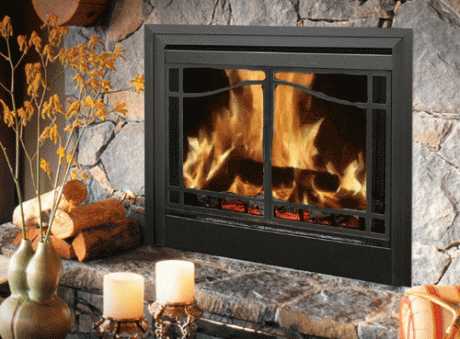
Пеллеты смогут заменить дрова
Первый этап – подготовка сырья
Например, фрезерный торф подсушивают сначала естественным образом, а затем очищают от примесей – камней, корней деревьев. Затем массу измельчают, отделяя от нее разнообразные включения, и отправляют на сушку.
В среднем, влажность сырья не должна превышать отметки в 12%. Как древесные пеллеты, так и другие виды топлива, требуют применения особых сушилок, исключающих возможность взрыва. После окончания сушки масса измельчается окончательно до необходимой фракции.
Второй этап – гранулирование
Теперь изготовление пеллет продолжается в участке гранулирования. В нем происходит формирование гранул. Изделиям придается цилиндрическая форма, а предваряет процесс гранулирования обработка сухим паром. Благодаря этому вещество становится более податливым, из него высвобождаются клеящие вещества.
Третий этап – охлаждение
Наконец, готовые топливные гранулы пеллеты отправляют охлаждаться. В это время происходит их высушивание и приобретение прочности. Мелкие частички, которые появляются в процессе транспортировки по технологическому циклу, отделяются из массы готовой продукции, чтобы придать ей товарный вид.
В зависимости от конечного потребителя, пеллеты могут укладываться в крупную тару или малые упаковки. Также транспортировка к покупателю иногда производится вагонами. Это бывает, если пеллеты предназначены для ТЭЦ или котельных.
Производство пеллет в домашних условиях
Именно из-за того, что производители пеллет чаще всего готовы делать выгодные предложения только оптовым покупателям, многие владельцы пеллетных котлов в частных домах задумываются о том, а не изготавливать ли топливные гранулы самостоятельно кустарным способом. Проблема заключается даже не в том, что расход пеллет в таком случае невелик. Скорее, сложности вызваны тем, что запасы топлива просто негде хранить, а арендовать специально под такие нужды складские помещения нерентабельно.
Вышеупомянутая технология производства достаточно сложна и требует определенных затрат. Например, именно при достижении низких показателей влажности гранулы способны отдавать большое количество тепла. Чтобы обеспечить качественную сушку, производителям приходится нести серьезные расходы. Даже если для домашнего производства не нужны большие объемы сырья, а, значит, и расходы на сушку будут меньше, необходимо обеспечить полную безопасность процесса, ведь опилки, торф или другие материалы в сухом виде легко воспламеняются.
Готовясь к домашнему производству пеллет, стоит понимать, что совершенно непросты и остальные стадии изготовления такого вида топлива. Речь идет и о сортировке, и очистке массы от примесей.
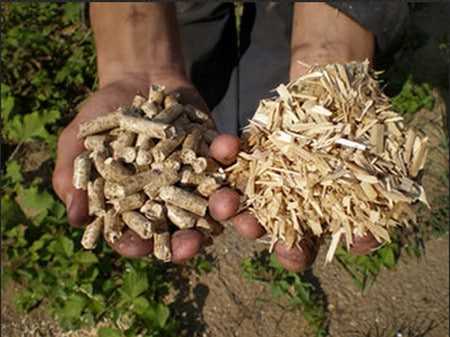
Изготовление пеллет из древесных опилок
Как сделать пеллеты из опилок
Посмотрев видеосюжет о пеллетах или почитав о них, у многих людей, живущих в частных домах, возникает желание наладить производство этого вида топлива хотя бы для собственного потребления. На первый взгляд все просто, особенно если есть возможность без особых затрат заполучить опилки или подходящее сырье. Но вникнув в суть технологического процесса и выяснив стоимость оборудования для производства пеллет, возникает вопрос, а можно ли в домашних условиях изготовить его. При большом желании, определенных навыках в сварных работах, смекалке и некоторых затратах, можно.
Классическая схема производства пеллет выглядит следующим образом: предварительное измельчение исходного сырья — просушка — более мелкое (не крупнее 2 мм) дробление — насыщение водяным паром пересушенного сырья до требующейся влажности (около 10%) — прессование с формированием пеллет — охлаждение пеллет — расфасовка.
В домашних условиях возможно производство пеллет, если исключить некоторые стадии классической схемы, т.е. если приобретать измельченное сырье, нужной влажности, к примеру, мелкие опилки деревообрабатывающих предприятий. В этом случае из оборудования понадобится только гранулятор. Если же пойти по полной схеме, то дополнительно потребуются сушилка и дробилка, в результате такие пеллеты станут слишком дорогими.
Как и из чего собрать гранулятор
Профессиональное оборудование имеет заоблачные цены, оно рассчитано на очень большую загрузку, что непросто обеспечить в домашних условиях. Да и в продаже его не так легко найти. Механизм, который необходим для изготовления пеллет, называется гранулятор. Сегодня можно купить как бывший в употреблении вариант, произведенный в странах Евросоюза, так и воспользоваться предложением местных инженеров, которые создают свои линии для производства топливных гранул. Но самым экономически выгодным вариантом будет изготовление гранулятора собственными руками.
Основными составляющими гранулятора являются электродвигатель, устойчивая основа, редуктор, шестерни с валом и матрица. Именно с последним элементом у многих возникают загвоздки. Как и из чего изготовить плоскую матрицу и подобрать под нее шестерни доступно показано в нижеприведенном видео.
Видео о том, как изготовить плоскую матрицу для гранулятора
Основу гранулятора — раму — можно сварить из стального профиля прямоугольного сечения не менее 40х25 мм. Размер ее будет зависеть от выбранной мощности электродвигателя. Последний придется приобрести. А вот редуктор можно изготовить самостоятельно, из чего и как неплохо расписано и продемонстрировано на фото здесь. Это, конечно, не единственный вариант.
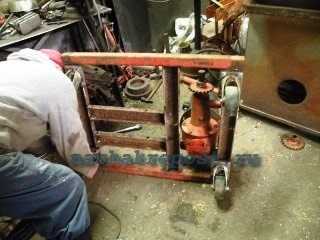
Гранулятор может быть мобильным, с колесиками на раме
Корпус гранулятора изготавливают из листового металла. Состоять он должен из двух частей: в верхнюю будут загружаться опилки, а в нижнюю они будут попадать, пройдя матрицу. Форма корпуса возможна только цилиндрическая, с диаметром, чуть большим, чем матрица для свободного вращения последней. В нижней части необходимо отверстие, желательно с желобом, чтобы готовые пеллеты свободно высыпались в некую емкость.
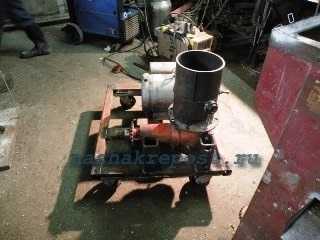
Гранулятор, собранный своими руками
Обе части корпуса приваривать нежелательно, чистить будет сложно. Их можно соединить болтами, предварительно сделав ушки. Вставляют в корпус матрицу и вал с шестернями. Гранулятор готов. Теперь древесные топливные гранулы для собственного пеллетного котла можно изготавливать дома.
101dizain.ru
Оборудование для производства пеллет
Сегодня в центре нашего внимания окажется такое перспективное и относительно молодое направление, как производство пеллет. Мы рассмотрим его технологические и конструктивные особенности, но главное – подробно и внимательно поговорим о том, какое стационарное и мобильное оборудование используется для производства пеллет и как собственно это оборудование выбрать.
Пеллеты. Что это и для чего они нужны?
Начнем с того, что определим, что же такое пеллеты, откуда они берутся и для чего используются. Пеллеты – это особым образом гранулированные отходы древесного производства (опилки, солома, кора деревьев, шелуха, оставшаяся от переработки зерновых и масличных культур). На западе общество уже давно пришло к необходимости переработки отходов любого производства и жизнедеятельности. Европейцы, американцы и азиаты сортируют мусор, собирают макулатуру и постепенно уходят от использования пластика. Что уж говорить о таком высоко отходном производстве, как лесная промышленность и древообработка?
Чего только не остается после распилки и обработки дерева. Это и стружки, и ненужная древесная кора и опилки. Логично, что все это богатство (в прямом и переносном смысле), нужно каким-то образом использовать. Самый широко известный путь – это направить опилки и стружку под пресс, где их, предварительно смешав с клеем, сформируют в ДВП, ДСП и МДФ-панели. Однако, как оказалось, это далеко не самый быстрый и дешевый способ. Гораздо легче эти же отходы гранулировать или “пеллетировать”.
Самые лучшие пеллеты получаются целиком из дерева. Но это экономически не выгодно, поэтому в качестве сырья используют прочие древесные отходы – кору, солому и пр. Чем больше в пеллетах “добавок”, тем ниже их ценность. Соотвественно, чем “чище” сырье для пеллет, тем они дороже и качественнее.
Условно пеллеты делятся на два класса по качеству: первоклассные и промышленные. Первоклассные пеллеты – те, где процент содержания побочных отходов древесного производства составляет меньше полутора процентов. Они имеют диаметр 0,6 – 0,8 см. и плотность около 600 кг/кубометр. Первоклассные гранулы выделяют 4,7 КВт/ч ( 16,9 МДж/кг). Их используют в качестве бионаполнителя для кошачьих туалетов, а также для отопления частных помещение (коттеджей, таунхаусов, загородных домов).
Промышленные гранулы – 0,8 -1,2 см. диаметром и плотностью 500 кг/кубометр. В них процент побочных отходов древесного производства составляет соответственно от полутора до пяти процентов. Из также используют в качестве бионаполнителя, но уже более дешевого, а также в качестве отопительного материала. При сгорании промышленные гранулы выделяют меньше, чем первоклассные – 4,2 КВт/ч. или 15,1 МДж/кг. Промышленные пеллеты не подходят для частных отопительных приборов, однако они тоже не остаются без реализации – их покупают организации для отопления небольших промышленных помещений при помощи специального оборудования.
Технология производства пеллет
Для того, чтобы из опилок получились гранулы не нужны большие производственные мощности и пространства. Достаточно грамотно подобрать оборудование для производства пеллет. Чтобы это было сделать проще, давайте разберемся, как вообще происходит “превращение” опилок в пеллеты.
Сначала древесные отходы (дальше – сырье) нужно хорошенько размельчить, раздробить в дробилках наподобие тех, что используются в зерновой обработке. Измельчают сырье до определенного стандартом размера, в зависимости от того, где будут использовать готовые пеллеты . Как только частицы достигают определенного объема (чуть больше кубического сантиметра) первичное дробление прекращается. В таком виде сырье легче высушить, поэтому его отправляют на сушку.
Для того, чтобы материал лучше спрессовывался он должен достигнуть определенной влажности – согласно технологическому стандарту не менее 8%, но и не более 12%. Сушка может быть барабанной (опилки погружают в барабан и постоянно крутят) или в виде поточной ленты (опилки высыпают на ленту и они сохнут естественным путем). Подбирать оборудование для сушки необходимо согласно выбранному типу будущих пеллет. Если предполагается производить первоклассные пеллеты, то подбирается специальное сушильное оборудование для производства древесных пеллет. Если нужны пеллеты производственного типа, то и сушка должна соответствовать характеристикам оборудования для производства пеллет из соломы.
Затем полуготовое, просушенное сырье необходимо измельчить на мельнице (часто молотковой) еще раз до определенного диаметра, как уже говорилось ранее. Чтобы получить гранулу диаметром 1,2 см. нужно положить сырье под пресс размером не больше 4 мм. Чтобы получить гранулу 0,6 см., сырье должно быть не больше 1,5 мм.
Если влажность сырья изменилась во время дробления, а точнее уменьшилась и стала менее чем 8%, его необходимо увлажнить, иначе, попав под пресс, оно просто напросто не склеится между собой. Увлажнение происходит паром или водой в зависимости от вида древесного сырья.
Далее – самый главный этап – гранулирование, оно же пеллетирование. Сырье попадает на пресс с матрицей определенной формы. Она может быть плоская или цилиндрообразная. Именно матрица и роллер являются основными в любом оборудовании для производства топливных пеллет и пеллет-наполнителей. Это первое и главное, на что следует обращать внимание при подборе необходимых станков и производственных комплексов. Если вам не безразлично качество продукта, которое вы получите, этим двум показателям нужно уделить как можно больше внимания. Учтите, что гранулирование/пеллетирование обязательно должно происходить при температуре до 90 градусов по Цельсию и под давлением, при чем под давлением не меньше, чем 300 атмосфер.
Ну и в конце, готовые пеллеты нужно остудить и просеять. К огромной радости любого изготовителя отходы от производства пеллет с легкостью можно направить на вторичную подготовку.
Оборудование. Особенности выбора
Теперь, когда вы ознакомились с основными технологическими и конструктивными особенностями производства пеллет, можно переходить непосредственно к выбору подходящего оборудования.
Реализовать вышеописанные производственный процесс можно двумя способами: закупить специализированное мини оборудование для производства пеллет или поставить у себя классическую производственную линию. Все мини-производства делятся на 3 типа в зависимости от источника энергии:
– машины на электродвигателе;
– машины на дизеле;
– машины от тракторного ВОМ;
Машины на электродвижке более стационарны, чем, например, агрегаты на дизеле, которые можно с легкостью перевозить непосредственно к месту лесозаготовки. Последний класс более удобен тем производителям, которые имеют свой трактор. Такие агрегаты также легко перевозятся или могут располагаться стационарно -в зависимости от потребностей производства. Электрические агрегаты вырабатывают от 200 до 550 кг/ч. Дизельные соответственно от 150 до 300 кг/ч. Агрегаты, работающие от ВОМ трактора, представляют некий средний вариант и обладают производительностью от 150 до 400 кг/ч. Понятно. что мини-производства не имеют некоторых этапов (сушка, влагообработка и т.д.), однако они дешевле и более мобильны.
В свою очередь настоящие комплексные фабрики по производству пеллет потребуют других затрат и больших производственных помещений, но и здесь есть свои преимущества – более качественные продукт и большие объемы.
При выборе полезно также обратить внимание на то, где производится желаемое оборудование. Ни для кого ни секрет, что лидер по выпуску оборудования для производства пеллет – Германия. Однако по отзывам неплохие агрегаты собирают в Италии. К слову сказать, отечественный рынок также конкурентоспособен в данном направлении, на ваш выбор агрегаты производства “Механика”, “Метком”, “Экоросс” и др. Главное, если завод изготовитель отказывает в посещении и не хочет отвечать на возникающие у вас вопросы -такие оборудование лучше не приобретать.
Ну и конечно, главное в выборе оборудование для производства пеллет – цена. Стоимость оборудования для производства пеллет колеблется от 4 700 до 13 200 долл. за мини-комплекс и от 13,2 тыс. долл до 40,8 тыс. долл за полноценную производственную линию. Но здесь, конечно, решать вам.
promplace.ru