Чем отличается ДСП от МДФ
ДСП и МДФ – часто встречаемые аббревиатуры. Попробуем разобраться, что они обозначают и, главное, чем отличаются друг от друга. Ведь ДСП и МДФ считаются наиболее популярными материалами, используемыми для производства дверей, корпусной мебели и прочих конструкций.
Определение
ДСП – древесно-стружечная плита. Формируется методом плоского горячего прессования древесных частиц (опилок и стружек), пропитанным связывающим веществом, главным образом, формальдегидными смолами. Сырьем для производства ДСП является малоценная древесина, как лиственных пород, так и хвойных. ДСП характеризуется повышенной прочностью, водостойкостью, превосходными тепло- и звукоизоляционными свойствами. Используется в мебельной промышленности, однако из-за входящих в ее состав формальдегидных смол не рекомендуется для производства детской мебели.
МДФ представляет собой древесно-волокнистую плиту средней плотности, для производства которой используют очень мелкие древесные опилки. Волокнистые плиты формируются из отходов деревообработки или предназначенного на вырубку леса, которые перемалывают не небольшие кубики, затем подвергают обработке паром, подаваемым под высоким давлением, и подают на диски терочной машины. Протертый материал поступает на сушку и последующую склейку. Древесные частицы склеивают парафином или лигнином, так что МДФ – исключительно экологичный материал. МДФ широко используется для изготовления дверей, мебели, ламинированных полов и погонажных изделий. Поверхность плит МДФ гладкая, однородная, ровная, плотная, легко поддается обработке.
Сравнение
Самое главное отличие между ДСП и МДФ состоит в технологии их производства. МДФ, в отличие от ДСП, изготавливают методом сухого прессования мелкой древесной стружки под действием высокого давления и температуры. Для производства ДСП применяют метод горячего прессования. Для формирования ДСП используют малоценные породы деревьев, в то время как для производства МДФ используют обрезки деревообработки либо древесину, предназначенную для вырубки.
Мелкодисперсная стружка склеивается парафином или лигнином, а при производстве ДСП для склеивания стружки применяют синтетические смолы. Таким образом, МДФ, в отличие от древесно-стружечных плит, считается экологически чистым материалом, который по своим экологическим характеристикам приближается к натуральной древесине. ДСП в процессе эксплуатации выделяет в воздух формальдегид (довольно токсичное вещество). Изделия из древесно-волокнистых плит могут эксплуатироваться в помещениях с влажностью воздуха до 80% (деревянные изделия – до 60%).
к содержанию ↑Выводы TheDifference.ru
- МДФ производят методом сухого прессования мелкой стружки под действием высокой температуры и давления, ДСП – методом горячего прессования.
- Для изготовления ДСП используют малоценные породы деревьев, для производства МДФ – обрезки деревообработки либо предназначенную для вырубки древесину.
- МДФ – экологичный материал, а ДСП в процессе эксплуатации выделяет в воздух формальдегид.
- МДФ, в отличие от древесно-стружечных плит, может применяться в помещениях с повышенной влажностью (до 80%).
thedifference.ru
Разница между мдф и дсп
Наибольшее распространение среди современных плиточных древесных материалов получили МДФ и ДСП. Они нашли широкое применение в изготовлении корпусной мебели, дверей, строительстве при возведении различных конструкций.
Выпускают плиты из древесных отходов, но с применением различных технологий и добавок. Из-за различий в производстве каждый плитный материал имеет свои характерные особенности, знание которых позволяет определиться с тем, какую плиту использовать для реализации поставленной цели.
МДФ
Древесноволокнистая плита средней плотности или сокращенно МДФ (от английского названия материала MDF — Medium Density Fiberboards) представляет собой экологически чистый материал с гладкой, легко поддающейся обработке, ровной поверхностью. Формируется волокнистый плиточный материал из мелкодисперсной древесной щепы методом сухого прессования.
Древесные отходы перемалываются, обрабатываются подающимся под высоким давлением паром и отправляются на диски терочных машин. Переработанный материал подвергается сушке и склейке. В качестве связующего компонента используется лигнин либо парафин — полимерные вещества, которые выделяются при нагреве древесины.
ДСП
Древесно-стружечная плита известна потребителю под аббревиатурой ДСП. В некоторых источниках этот композиционный листовой материал обозначается сокращением ДСтП. Получают материал методом плоского горячего прессования коры, отходов некондиционных изделий, опилок, технологической щепы, горбыля. Сырье используется неценное, полученное от хвойных либо лиственных пород.
Древесная масса измельчается и смешивается с термореактивной смолой, отправляется под пресс для отверждения, а после охлаждения нарезается на плиты необходимого размера. В производстве ДСтП используют связующее вещество неминерального происхождения, как правило, формальдегидные смолы.
В чем заключаются отличия между ДСтП и МДФ?
Плиточные материалы имеют различные показатели прочностных характеристик, технологичности и безопасности. Они определяют главные отличия между древесно-стружечными и древесноволокнистыми плитами.
Различаются плиты не только физическими и эксплуатационными качествами, но и поверхностью. В необработанном виде, то есть без покрытия, МДФ имеет гладкую и однородную поверхность, а у ДСП, наоборот, даже в торцах можно увидеть древесную «начинку».
Прочностные характеристики
Средняя плотность MDF составляет от 720 до 870 кг на куб. м. Этого достаточно, чтобы обеспечить длительный эксплуатационный срок и высокую устойчивость материала к износу. Механические показатели и влагостойкость древесноволокнистых плит превосходят даже многие породы натуральной древесины.
Прочность плит ДСтП зависит от того, к какой группе принадлежит материал: с низкой — 350-650, средней — 650-750 либо высокой плотностью— 750-800 кг/м3. Это означает, что в целом древесно-стружечные материалы уступают по прочности древесноволокнистым.
Экологичность и безопасность
ДСП уступает МДФ по экологичности. Если плиты не имеют облицовки либо повреждены, они будут выделять в окружающее пространство вредный для организма человека формальдегид. Это накладывает определенные ограничения по использованию древесно-стружечных материалов.
В зависимости от показателя эмиссии формальдегида, различают три класса экологичности древесно-стружечных плит, обозначаемых E0, E1 и E2. Первые два класса отличаются большей экологичностью, а третий недопустим к использованию для производства детской мебели.
Технологичность и возможность обработки
Размер фракций и однородность состава, используемого для формирования плит MDF, наделяет материал идеально ровной и гладкой поверхностью, которая полностью готова для нанесения декоративного либо облицовочного материала. Такой поверхностью среди стружечных плит обладает только отшлифованная марки П-А.
Высокая твердость ДСП не позволяет проводить тонкую обработку, например, глубокую фрезеровку, наносить фигурные элементы и детали. Это значительно снижает декоративность готового изделия. Материал хорошо поддается пилению, сверлению, строганию и другим видам механической обработки. Отдельные элементы из ДСтП могут склеиваться между собой, скрепляться шурупами и гвоздями.
Преимущества и недостатки плиточных материалов
МДФ по многим показателям лучше ДСП, если сравнивать экологичность, прочность, технологичность этих материалов. Но, независимо от этого, большей популярностью пользуется именно стружечная плита.
Практически во всех сферах применения плиточных материалов именно ДСтП занимает лидирующие позиции. Все это обусловлено преимуществами, которые присущи этому материалу.
Достоинства ДСП
- доступность выбора;
Выпускают стружечные плиты отечественные и зарубежные производители. Конкуренция и отсутствие дефицита делает материал доступным.
- низкая стоимость;
Сырье для ДСтП получают из малоценных пород. Это позволяет получать достаточно дешевый плиточный материал, значительно снижать стоимость готовых изделий, выпускаемых из него.
- влагостойкость;
Это преимущество присуще не всем плитам ДСП, а влагостойким. Они используются для производства изделий и конструкций, которые будут эксплуатироваться в условиях повышенной влажности.
Недостатки ДСтП
Есть у материала и минусы, но они в большей степени обусловлены низким качеством плит и несоблюдением технологии производства:
- плохо поддается обработке, держит фурнитуру и крепежные элементы при повторном вкручивании;
К этим недостаткам приводит нарушение в соотношении между сырьем, полученным из лиственной и хвойной древесины, которое должно быть равно 10:90. ДСтП плохого качества получается и в тех случаях, когда плиты формируют с использованием коры, корней и сучков. Недостаток древесной массы недобросовестные производители компенсируют увеличением содержания формальдегидных смол.
- низкая экологичность;
Если стружечные плиты предназначены для применения в помещениях жилого назначения, необходимо выбирать материал классов E0 либо E1. Испарения формальдегида в них варьируется в пределах 0-10 мг на 100 грамм композита. Уменьшает выделение вредных веществ качественная герметизация торцов и облицовка поверхности плит. Все это позволяет приобрести материал, который безвреден для человека и окружающей среды.
Плюсы и минусы МДФ
Древесноволокнистые плиты отлично удерживают крепежные элементы и фурнитуру. Это достигается благодаря высокой плотности материала. МДФ не боится влаги, легок в обработке. На его поверхности выполняют округлые элементы, филенку, фигурные фрезеровки.
Многочисленные преимущества MDF не сделали его лидером среди плиточных древесных материалов. Его плюсы не могут компенсировать такие недостатки, как высокая стоимость и воспламеняемость. Использование древесноволокнистых плит нерентабельно в строительстве, а работать с ними вблизи открытого огня опасно.
Область применения ДСтП и МДФ
Каждый материал имеет как недостатки, так и преимущества. Выбор между стружечными и древесноволокнистыми плитами зависит от того, для каких целей их предполагается использовать.
ДСП применяют при возведении межкомнатных перегородок. Плиту можно пилить, сверлить и окрашивать. Это делает ее востребованной в оформлении интерьеров. Стружечные плиты используются в производстве корпусной мебели бюджетного класса. Высокая прочность материала позволяет использовать его при обустройстве пола.
Древесноволокнистые плиты средней плотности широко применяются в производстве фасадов, наличников, дверей. Если финансовые возможности позволяют, перегородки лучше возводить из экологически чистого МДФ.
Предметы мебели средней ценовой категории с красиво и изящно оформленными фасадами выпускают именно из этого плиточного материала. Мебель для детских комнат тоже по причине экологичности должна быть выполнена не из ДСП, а из МДФ.
Инстаграм
superarch.ru
ДСП или МДФ – что лучше выбрать для изготовления мебели?
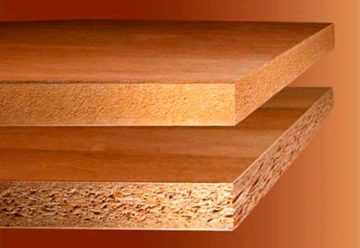
ДСП и МДФ изготовляются на основе древесины, поэтому во многом схожи. Но кроме стоимости, есть и ряд существенных отличий. Только разобравшись в них, можно сделать вывод, что же в конкретной ситуации в процессе строительства (ремонта, реставрации) использовать все-таки лучше – ДСП или МДФ. Кстати, это относится и к выбору мебели. Ее прочность и долговечность – вот основные критерии оценки, так как приобретается она на долгие годы.
Расшифровка аббревиатуры
- ДСП. Первые две буквы обозначают особенность сырья (древесно-стружечная). То есть в производстве используется не пыль, как при изготовлении некоторых разновидностей стройматериалов, а достаточно крупные фракции. Последняя литера указывает на тип изделия (плита).
- МДФ. Путаница в расшифровке связана с тем, что при отображении маркировки английская фразеология проставляется русскими буквами. По сути, это тоже плита, но несколько иная по структуре – древесноволокнистая. То есть исходный материал на этапе подготовки подвергается более тщательному измельчению.
Чтобы понять, что из двух разновидностей однотипной продукции лучше (ДСП или МДФ), следует разобраться, в чем их отличие по эксплуатационным характеристикам. Именно это и определяет специфику применения каждого из образцов.
Особенности материалов
Все обозначенные ниже достоинства плит, а также ряд недостатков – результат анализа отзывов, обмена мнениями на тематических форумах. С точки зрения автора, они заслуживают большего доверия, чем информация, размещенная на сайтах дилеров и производителей. По крайней мере, заказными их точно никак не назовешь.
ДСП
Подготовленная смесь на основе фракций древесины (стружка, опилки) и клеящего состава подвергается «горячему» прессованию, то есть одновременно воздействию высоких давлению и температуры. И вот тут есть одно из главных отличий от МДФ. Частицы дерева различаются размерами, формой. Кроме того, есть разница и в долевом соотношении компонентов, виду используемого клея. Исходя из этого, все плиты ДСП по плотности структуры делятся на группы – с малой, средней и высокой. То есть выбор для покупателя по данному критерию есть.
Образцы могут состоять из одного или нескольких слоев (до 5), что также разнообразит их сортамент.
В зависимости от количества токсичного формальдегида (один из компонентов клея) в исходной смеси для ДСП плиты подразделяются на категории Е0 (минимальный процент, который на практике не учитывается), Е1 (небольшое содержание) и Е2 (повышенное).
Плюсы:
- Большой сортамент продукции, что позволяет сделать оптимальный выбор ДСП.
- Привлекательная стоимость. По сравнению с МДФ при всех равных параметрах плит (габариты, толщина) она ниже примерно на 30 – 35%. Это отчасти вызвано тем, что в этом сегменте рынка конкуренция значительная, и с целью увеличения сбыта производители вынуждены снижать цену на листы ДСП.
Минусы:
- Токсичность. Возможно, это чрезмерно резкое определение, но то, что практически во всех клеящих составах для этой разновидности плит присутствует формальдегид – однозначно. Следовательно, при нагреве смолы выделяют вредные испарения. Разница – лишь в их концентрации (в зависимости от категории ДСП и местных условий).
- «Рыхлость» структуры. Даже если плотность ДСП максимальная (820 кг/м3), то многократный монтаж/демонтаж этих плит не рекомендуется. После нескольких переустановок крепеж в посадочном гнезде постепенно начинает расшатываться, что резко снижает надежность сборки. Поэтому для изготовления мобильных (переносных) конструкций ДСП использовать нецелесообразно. В крайнем случае, для задних стенок различных шкафов, стеллажей и тому подобное, где можно высверливать новые отверстия сколько угодно – все равно от визуального обзора они будут скрыты.
- Сложность обработки. В процессе раскроя, тем более, если неправильно подобран инструмент, получается не просто широкий рез, но и с бахромой на кромках. Фрезеровка, выборка пазов на ДСП вообще не рекомендуется. Самостоятельно, не имея практических навыков, добиться высокого качества не удастся. Это нужно учесть тем, кто решил своими руками изготовить из этих плит какой-либо предмет меблировки.
- Низкая прочность на изгиб. Здесь коротко – даже ДСП с высокой плотностью довольно легко (при определенных условиях) ломаются. Поэтому применение в местах, подвергающихся динамическим воздействиям, использовать не стоит. Только для «стационарных» конструктивных элементов.
МДФ
Условия изготовления во многом схожи с ДСП (горячий пар, прессование), но технология несколько отличается. Отходы деревообработки измельчаются, после чего еще и подвергаются протирке на специальном оборудовании. По сути, это уже микроскопические фракции, пылевидная масса. После просушки производится ее смешивание с клеящим составом и прессование. Поэтому говорить о каких-то слоях не приходится – по своей структуре плиты МДФ однородны и отличаются повышенной плотностью (790±50).
«Экологичность». При изготовлении МДФ смолы с содержанием токсичных компонентов не используются. Все – только натуральное (фракции древесины + клеящие составы на основе лингина, парафина или чего-то подобного), без «химии».
Точность всех линейных параметров. Прессовка «пыли» позволяет практически полностью исключить отклонения от заявленного размера. Кроме того, грани и торцы плит получаются гладкими, поэтому перед дальнейшей отделкой не нужно заниматься дополнительной шлифовкой такой основы. Как результат – частичное снижение затрат на монтаж (сборку) и экономия времени.
Плюсы:
- Простота обработки. МДФ, в отличие от ДСП, можно фрезеровать, делать различные выборки, сверлить. В процессе раскроя – ровный рез, высокая точность и минимум отходов.
- Высокая прочность. В результате – возможность сооружения сборных конструкций. Как материал для мебели (с учетом небольшой стоимости продукции), особенно при изготовлении ее своими руками, МДФ – один из лучших вариантов.
- Относительная пластичность. По этому параметру данные плиты превосходят ДСП. При незначительной деформации конструкции, равно как и чрезмерной нагруженности образца, МДФ не сломается, а лишь слегка прогнется (если изначально толщина подобрана правильно).
- Хорошая влагостойкость. Если в сырых помещениях ДСП долго не прослужит, то МДФ использовать можно. Тем более, если плита с ламинированием.
Минусы:
- Воспламеняемость. И ДСП, и МДФ, как материалы на основе древесины, подвержены горению. От этого никуда не деться. Но с плитами древесноволокнистыми в этом плане нужно быть аккуратнее. Они сильнее реагируют на открытый огонь. Поэтому при монтаже и отделке МДФ его использовать нельзя (в виде газовых горелок или чего-то подобного). К примеру, при фиксации на такой основе самоклеящихся полотен рулонных материалов.
- Низкая прочность на удар. Несмотря на определенную пластичность плиты, упавший тяжелый предмет оставляет на МДФ вмятину. Устранить такой дефект довольно сложно. Поэтому для чистовой отделки полов эти изделия лучше не применять.
- Стоимость выше, чем ДСП. Это ограничивает использование МДФ в различных подсобках и так далее. То есть там, где внешний вид особой роли не играет, лучше ориентироваться на ДСП соответствующей категории.
Вывод
Прочность
По верхнему пределу данного параметра, если речь идет о нагруженных конструкциях, существенной разницы между ДСП и МДФ нет. Однако для других целей (менее ответственных элементов) выбор ДСП значительно шире, так как численные выражения этой характеристики лежат в достаточно большом диапазоне (значение плотности от 350 до 820 кг/м³). А так как это напрямую сказывается на стоимости продукции, то грамотный расчет и выбор образца требуемой группы позволяет вести речь о возможности оптимизации расходов.
Степень обработки граней
С одной стороны, чем мельче фракции, тем более гладкая получается поверхность. Если рассматривать с этой точки зрения, то МДФ лучше. Хотя есть и модификации ДСП, которые отличаются великолепным внешним видом. Они имеют в аббревиатуре обозначение (через тире) из литер П-А. Это плиты отшлифованные, поэтому их перед нанесением лака или оклеиванием дополнительно обрабатывать не нужно.
«Экологическая чистота»
Нередко покупатели обращают внимание на токсичность тех или иных стройматериалов, и правильно делают. От этого во многом зависит, стоит ли использовать продукцию в жилом помещении или нет. В этом плане преимущество у МДФ. Такие плиты даже при значительных температурах (например, на кухне) практически не выделяют вредных компонентов. А вот с ДСП следует быть аккуратнее. Они главным образом применяются при обустройстве различных подсобок или надворных построек (стеллажи в гаражах, сараях, поверхностная облицовка и тому подобное). Для жилых – в отдельных случаях, и то, продукция, в маркировке которой присутствует обозначение категории Е0 или 1.
При этом рекомендуется организовать дополнительную защиту от выделения токсинов поверхностным покрытием (пленкой, лакокрасочными составами или чем-то еще). Причем обрабатываются все грани плиты ДСП, включая и ее торцевые части (особенно после раскроя образца).
Остается добавить, что для снижения стоимости работ целесообразно прибегнуть к комбинации материалов. То есть видимую часть конструкции изготовить из МДФ, а ту, что скрыта (задняя стенка, внутренние перегородки отсеков и тому подобное) – из ДСП. Именно так в основном и поступают рачительные «домашние мастера».
Ну а что именно выбрать – ДСП или МДФ – следует решать, исходя из специфики применения. Если учесть затраты на плиты, все нюансы их подготовки, монтажа и длительность дальнейшей эксплуатации в конкретных условиях, то определить, что в данном случае лучше, совсем не трудно.
woodguide.ru
характеристики, описание, свойства — Идеи интерьеров
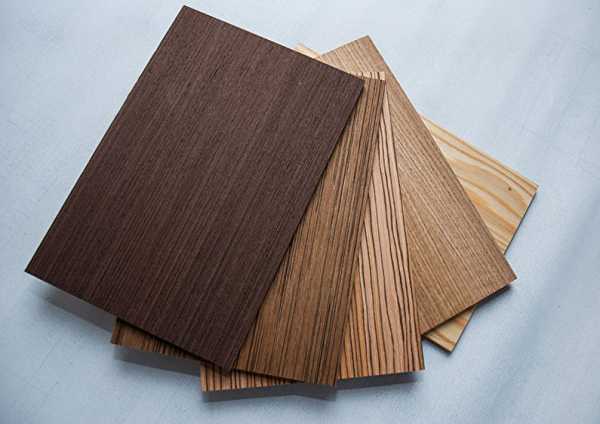
Планируя ремонт или покупку мебели, всегда хочется узнать больше о существующих материалах, их преимуществах и недостатках. Обладая исчерпывающей информацией, легче понять, для каких условий эксплуатации предназначены те или иные вещи, рассчитать примерный срок службы и сделать осознанный выбор. В этой статье речь пойдет об МДФ – заменителе массива дерева, который часто путают с древесностружечными плитами. Обладая рядом преимуществ, о которых будет рассказано ниже, этот материал отлично подходит для строительства, отделки помещений, производства мебели, дверей и декора.
Что такое МДФ?
Аббревиатура МДФ — это транслитерация англоязычного термина Medium Density Fibreboard, что в переводе означает «волокнистая плита средней плотности».
Данный материал состоит из прессованных измельченных опилок, смешанных со связующими веществами. Выпускается он в листах толщиной от 3 мм до 6 см. Из древесноволокнистых плит изготавливают мебель, строительные и отделочные элементы, упаковку и другие вещи. Фактически, это недорогой заменитель дерева, производимый из отходов лесной промышленности.
Обрабатывать МДФ намного проще, чем натуральные доски, к тому же, он не усыхает, не трескается, прекрасно сохраняет тепло и обладает хорошими звукоизолирующими свойствами. В сравнении с древесностружечными плитами, этот материал более экологичен, так как в нем содержится гораздо меньше формальдегидных смол.
К недостаткам МДФ можно отнести неустойчивость к влажности и механическим воздействиям, а также быструю возгораемость. Срок эксплуатации изделий из МДФ в нормальных условиях составляет около 10 лет.
Как производят МДФ панели
Иногда МДФ расшифровывают как «мелкодисперсная древесная фракция» и это вовсе не ошибка.
Дело в том, что для производства данного материала сырье (щепки, стружку, опилки) тщательно измельчают, превращая почти в пыль. Для этого их сначала нагревают паром до 100°C и доводят до влажности 80%, после чего помещают в дефибратор и перемалывают. К волокнистой массе добавляются модифицированные меламином карбамидоформальдегидные смолы и парафин. Далее все это сушится несколько секунд горячим воздухом при средней температуре 200°C и попадает в бункер для утрамбовки.
Получившуюся смесь разравнивают катком по конвейеру, формируя непрерывную плиту. Затем сверху опускают пресс с давлением 350 МПа и нагревают материал до 230°C. Под таким воздействием он сплавляется, уплотняется и приобретает прочность. Впоследствии давление уменьшают примерно в три раза, а толщину листа регулируют уже без нагрева.
Остывшую полосу шлифуют и разрезают пилой на плиты. На последнем этапе наносится декоративное покрытие.
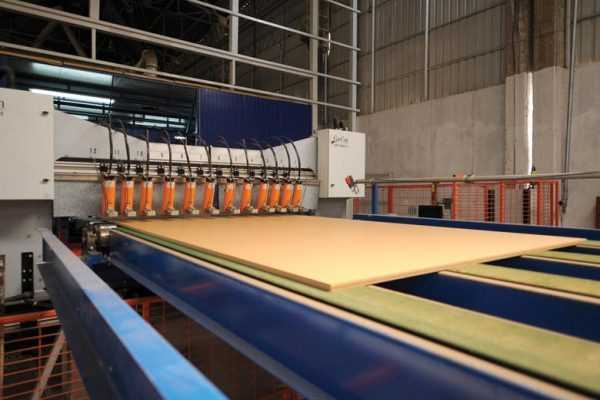
Виды МДФ панелей
Средней плотности волокнистые плиты, которые применяются для производства мебели и лицевой отделки помещений, в зависимости от типа декоративного покрытия подразделяются на ламинированные, крашенные и шпонированные.
Ламинированные
Ламинирование подразумевает горячую поклейку на поверхности МДФ какого-либо декоративного материала. Это может быть просмоленная бумага, меламин, а чаще всего — пвх-пленка. Лицевой материал плотно сцепляется с основанием под прессом, благодаря чему обеспечивается высокая эстетичность плит на весь период пользования. Существует огромное количество текстур ламината — под камень, кожу, слоновую кость, различные ткани, но самыми популярными являются имитации древесины.
Крашенные
Применение современных лакокрасочных составов поверх выравнивающего слоя грунтовки позволяет делать из сероватых листов МДФ сверкающие зеркально-глянцевые или благородные матовые панели. Такая обработка зачастую применяется для кухонной мебели (которую важно защитить от влаги), а также других интерьерных элементов в стиле модерн, хай-тек и минимализм.
Шпонированные
Шпон — это тонкий, красивый срез натурального дерева. Он приклеивается на плиту, придавая ей полное внешнее сходство с оригиналом. Шпонированные панели МДФ используются для изготовления дверей, стенок, комодов и огромного количества других вещей.
В целом, это, наверное, самый дорогой вид отделки, хотя стоимость зависит от качества самого покрытия. По виду и на ощупь это настоящая древесина, иногда даже редких, необычных пород.
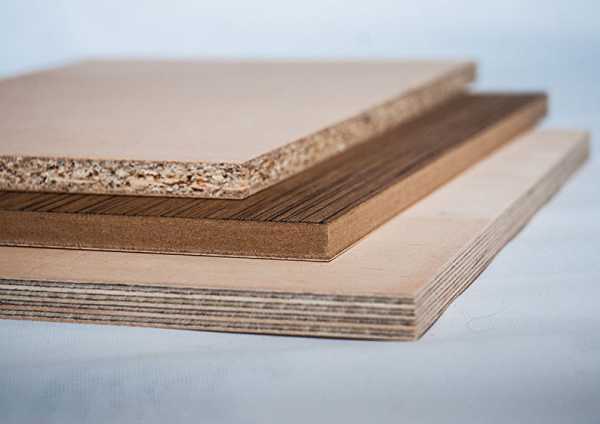
Свойства и характеристики МДФ панелей
Древесноволокнистые плиты пользуются в современном мире не меньшей популярностью, чем природные доски. Для этого существует целый ряд причин, а именно:
— прочность — между волокнами спрессованных листов нет воздуха, поэтому материал не растрескивается и не крошится, долго держит форму;
— простота обработки, в том числе декоративной — из МДФ легко выпиливать любые фигуры, вырезать объемные украшения и даже по специальной технологии придавать ему мягкие изгибы;
— большой выбор лицевых покрытий, который позволяет найти идеальный вариант для любого интерьера.
После пропитки специальными веществами, ламинирования пленкой или покрытия латексной водоотталкивающей краской, МДФ можно использовать даже во влажных помещениях, таких как ванная и кухня. Изделия с маркировкой E1 допускаются для применения в жилых комнатах (это значит, что 100 грамм плиты выделяют не более 10 мг формальдегидов, то есть допустимую по санитарным правилам норму). В любом случае, из ДСП вредных испарений в несколько раз больше.
МДФ панели бывают I класса (без изъянов) и II (возможны небольшие эстетические недостатки, неровности или чуть более крупные вкрапления).
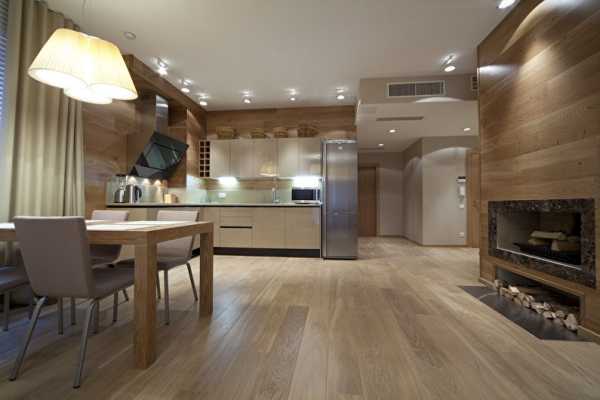
Применение МДФ
Мебель
Изделия из древесноволокнистых плит средней плотности — настоящая находка для всех желающих обставить свой дом, офис или общественное заведение красивой и качественной мебелью за сравнительно небольшую цену.
Как правило, МДФ применяют для корпусных вариантов — шкафы, гарнитуры, стеллажи, столы, тумбочки, комоды из этого материала выглядят очень современно и прекрасно выполняют свои функции.
Впрочем, нередко он составляет и основу диванов, мягких кресел, кроватей. Покрытая ламинатом или шпоном, с рельефными узорами или интересно окрашенная, мебель из МДФ поможет где угодно создать уютную и теплую атмосферу.
Строительство и ремонт
МДФ отлично справляется с ролью универсального заменителя дерева и при обустройстве зданий. Из таких плит делают балки, перегородки, обшивают ими потолки, утепляют стены, изготавливают плинтуса, уголки, дверные коробки, двери, лестницы, перила и подоконники.
А вот где применять такие панели не стоит, так это на полу (они довольно мягкие и могут деформироваться), а также в наружной отделке и в помещениях с очень высокой влажностью.
Вырезать любую форму или выпилить узор из МДФ не составляет труда даже для тех, кто никогда не работал с деревом и не имеет специальных станков. Это занятие чем-то напоминает обработку гипсокартона.
Производя манипуляции с МДФ стоит помнить, что он не допускает многоразового применения саморезов и гвоздей. Если нужно сделать подобное крепление, в материале сначала просверливают отверстия, а затем уже с помощью болтов и гаек соединяют элементы.
trizio.ru
МДФ. История создания МДФ
MDF – Medium Density Fiberboard, что в переводе с английского означает «среднеплотное волокнистое покрытие». МДФ — плитный материал, изготавливаемый методом сухого прессования мелкодисперсной древесной стружки при высоком давлении и температуре.
Прототип древесноволокнистой плиты впервые был получен Уильямом Генри Мейсоном, изобретательным инженером из США. В 1924 году он упорно занимался созданием технологии производства картона или, хотя бы, фанеры из отходов лесопильных предприятий – опилок, стружки и щепы. Первая задача – разделение бросовых фрагментов древесины на волокна – более-менее успешно ему удалась. Мейсон создал «паровую пушку», позже названную его именем – труба из стального сплава, с одного торца полностью заварена, с другого имеющая сдвижную крышку, снять которую можно было удаленно. Работала пушка Уильяма Мейсона так – после закладки мелкой щепы и стружек внутрь, залива нескольких литров воды, свободное отверстие плотно затворялось крышкой. Ближе к «заваренному» концу трубы изобретатель размещал газовую горелку – пламя нагревало воду, превращая ее в пар. Выждав, пока давление не достигнет определенного значения, Мейсон тянул за ручку и сдвигал крышку – стремясь уровнять давление, пар вместе с частицами древесины мощным потоком выбрасывало из ствола «пушки» на предварительно выставленный напротив приемный бункер. В результате значительная часть стружек и пр. разделялась на волокна.
Воодушевленный успехом, Мейсон принялся работать над производством бумаги. Однако ни бумаги, ни даже картона из древесных волокон создать не удалось – даже в расслоенном состоянии древесные частицы были чрезмерно крупны. Не привыкший сдаваться просто так, Уильям Мейсон переориентировался на получение древесной плиты, которую можно было приспособить под стройматериал. Арендовав паровой пресс старой модели, американский изобретатель поместил древесные волокна на его нижнюю плиту, аккуратно распределив их в форме ковра. Поскольку эксперимент проводился из волокон, полученных при помощи «пушки» с утра, их укладку Мейсон планировал к обеду. Он рассчитывал запустить пресс на полтора-два часа, не более, но голод вынудил его оставить эксперимент и отправиться домой на обед. И если бы не две ошибки, допущенные в тот день Уильямом Мейсоном, то древесноволокнистые плиты были бы созданы значительно позже – инженер не проверил все узлы старого пресса на исправность (паровой клапан на верхней прижимной плите протекал) и позабыл отключить пресс перед тем, как направиться к обеденному столу. А путь от лесопилки, где проводились исследования, до дома инженера был не близок…
Древесноволокнистый ковер находился в прессе под воздействием давления и пара длительный срок. После плотного обеда Мейсон вернулся на лесопилку и заметил, что паровой пресс по-прежнему работает, что из щели между плитами выходит пар, но то, что он увидел после отключения прибора и подъема ползуна (верхней, подвижной плиты), привело изобретателя в восторг. Под воздействием раскаленного пара и давления древесный лигнин склеил волокна в достаточно плотную плиту, не разрушающуюся при подъеме за один из краев. Вскоре Уильям Мейсон запатентовал «масонит», как он назвал изготовленную древесноволокнистую плиту. Кстати, масонит производится по сей день – в России такие плиты, с одной стороны гладкие, а с другой шероховатые, называются оргалит (ДВП).
До середины XX века потребности в плитах из древесных волокон не существовало, хотя их технологические компоненты – тот же масонит Мейсона и первая фенолформальдегидная смола «бакелит» химика Лео Бакеланда – были уже известны промышленникам. Серийный выпуск плит MDF стартовал в США ближе к концу 60-х, причем одновременно на нескольких предприятиях, принадлежавших различным компаниям. Все производители использовали в те годы схожую технологию выпуска древесноволокнистых плит, с уверенностью назвать среди них первую компанию-изготовителя не представляется возможным.
В Советском Союзе “толстые” плиты из древесных волокон не производились – считалось, что древесно-стружечных плит (ДСП) более чем достаточно. С ориентацией на российскую мебельную промышленность первое производство отечественных древесноволокнистых плит стартовало в поселке Шексна (Волгоградская обл.) в 1997 году. С начала XXI века Китай – мировой лидер в производстве плит MDF, а также мебели и прочих изделий из этого материала.
Технология производства МДФ плит
Первый и повсеместный метод изготовления плит из древесных волокон был «мокрым» и мало чем отличался от техники выпуска картонных листов. Впоследствии была разработана технология, позволяющая обходиться без воды – именно ее используют производители MDF сегодня. Рассмотрим этапы «сухого» выпуска древесноволокнистых плит средней прочности.
Заготовка щепы. Породы древесных стволов, поступающих на производство МДФ плит, могут быть различными – в составе одной и той же плиты, как правило, волокна нескольких деревьев. Лес-кругляк помещают в станки барабанного типа, в процессе вращения которых встроенные ножи полностью срезают и удаляют кору. Далее, в дезинтеграционных машинах, оснащенных массивными рубящими ножами, окоренный кругляк становится щепой. Помимо разделки древесины на щепу, рубка снижает связи между волокнами, которые обеспечивает древесный полимер лигнин. Нарубленная щепа поступает на конвейерную ленту и следует под несколькими электромагнитами, извлекающими из нее частицы металлов. Следом щепу сортируют в виброситах – излишне крупная вновь идет на рубку, чрезмерно мелкая щепа поступает в бункер-накопитель отходов и затем будет сожжена в печах котельной. Древесные частицы необходимого диапазона размеров направляется на мойку в циклоны вертикальной установки – в них из щепы устраняется мусор и примеси минералов. Подготовленная к следующей операции – обработке паром – щепа следует в бункер, где прогревается до температуры в 100°С с доведением степени ее влажности до 80% по всему объему.
Получение древесного волокна. Горячая и влажная щепа загружается в специальную установку – дефибратор (второе название – рефинатор) – размалывающий аппарат дискового типа. Шнек питателя прогоняет частицы древесины через каскад лопаток дисковой и конической формы, разделяя их на волокна. Операция деления повторяется два-три раза, для этого необходимое число установок-дефибраторов выставляются друг за другом в единый каскад. Для более эффективной разбивки щепы на волокна в емкость дефибраторов закладываются фенолформальдегидные смолы, парафин, связующие материалы и отвердители.
Полученные в дефибраторах древесные волокна направляются в сушилку, в процессе следования они постоянно обрабатываются паром. Внутри сушилки на волокна воздействует уже не пар, а сухой воздух, имеющий температуру в диапазоне от 170 до 240°С – срок сушки короток, не превышает 5 секунд. Осушенные волокна древесины (влажность не более 9%) загружаются в циклон, задача которого – вывести из массы волокон избыточный объем воздуха. Волокна, готовые к производству древесноволокнистых плит, накапливаются в бункере.
Образование ковра и прессование плит МДФ. При движении по конвейеру древесным волокнам придается форма непрерывного ковра, для чего поток волокон прикатывается роликами (см. фото).
Первичное прессование волокнистого ковра проводится при помощи обычного пресса и преследует одну цель – полностью устранить из будущей MDF плиты воздух. По окончании этой операции выполняется основное прессование (горячее), проходящее в три этапа:
придание плите поверхностной жесткости. Под давлением около 350 МПа, развиваемым плитой-ползуном и при температуре в 200-230°С древесноволокнистый ковер приобретает первичные свойства плиты МДФ;
упрочнение внутреннего слоя плиты. Давление в прессе снижается до 50-120 МПа, температура нагрева – до 190-210°С, в результате связующие компоненты в составе уплотненного ковра из древесных волокон формируют прочные связи внутри изделия;
калибровка древесноволокнистой плиты. Сформированную плиту необходимо довести до требуемой толщины, для чего ее опрессовывают под давлением в 60-150 МПа без нагрева.
Готовая плита МДФ непрерывной полосой выходит из-под калибровочного пресса, далее ее нарезают на блоки заданных размеров циркулярными пилами. Разрезанные плиты укладываются на стеллажи для охлаждения, на эту операцию уходит порядка 25 минут. Несмотря на серию прессовочных работ плиты MDF все же имеют некоторые поверхностные изъяны и небольшой, в несколько миллиметров, перепад по толщине. Их устраняют на плоскошлифовальных станках. Готовая продукция маркируется и помещается на склад, либо следует в цех, где поверхностям плит придается декоративная отделка.
Характеристики МДФ
Госстандарта России на древесноволокнистые плиты средней плотности не существует, производители МДФ либо разрабатывают собственные технические условия, либо выпускают плиты по европейскому стандарту ANSI A208.2. Производятся плиты МДФ первого и второго сорта, толщиной от 6 до 24 мм. Cклеивание древесных волокон осуществляется при помощи карбамидоформальдегидных смол и древесного лигнина. Многими производителями в качестве связующего элемента заявляется только лигнин: мол, никаких экологически вредных компонентов не присутствует — это неправда, МДФ панелей и плит, созданных только при помощи лигнина, в действительности не существует. Стандартные размеры панелей МДФ: 1650 на 1650 мм, 2800 на 1650 мм, 2750 на 1650 мм, 2 250 на 1650 мм и 2440 на 1650 мм. Также производятся панели «дополнительных» размеров — 3660 на 1650 мм, 3050 на 1650 мм, 2100 на 1650 мм и 1850 на 1650 мм. Поверхности панелей МДФ I сорта не имеют ровным счетом никаких дефектов — они идеально ровные, без сколов, царапин и каких-либо пятен. Плиты II сорта могут иметь царапины глубиной не более 0,3 мм и не длиннее 20 мм, небольшие сколы на кромках, небольшие по площади дефекты шлифовки. МДФ III-го сорта подходит только лишь для строительных нужд, т.к. имеет множественный сколы и дефекты поверхностей. Плотность выпускаемых плит МДФ лежит в пределах от 600 до 1200 кг/м3. Класс эмиссии (выделение свободного формальдегида со 100 г массы) для любого сорта МДФ — E1, т.е. не превышает 10 мг. Любая панель МДФ обладает высокой влагостойкостью и чем толщина панели больше, тем более высока ее влагостойкость — максимальное разбухание для плит толщиной 6-8 мм не превышает 17% от исходного объема МДФ. В процессе производства плитам МДФ могут быть приданы более высокие качественные свойства по водостойкости, огнестойкости и биостойкости, чем у серийных плит.
Применение МДФ
МДФ – очень плотный и однородный материал, что делает его устойчивым к влаге и горячему пару, грибкам и микроорганизмам. Именно поэтому плиты МДФ широко используются при изготовлении кухонной мебели, ведь они очень хорошо переносят воздействие кухонного пара, не разбухают, не коробятся. Разработанная техника гнутья конструкционных элементов из склеенного древесного волокна позволила создавать из этого материала кресла и стулья, изящные спинки кроватей. Как правило, вся мебель для помещений с высокой атмосферной влажностью (санузлов, кухонь) выполняется из шпонированного или ламинированного МДФ. Плиты из МДФ также могут применяться для устройства межкомнатных перегородок, но для настила полов они не пригодны вследствие их механической уязвимости. Панели из этого материала широко используются в декоративном оформлении интерьеров — в отделке потолков и построении воздуховодов. МДФ используют для изготовления дверных блоков вместе с коробами и наличниками из того же материала. Из МДФ изготавливают ламинированные наличники и накладки на входные двери. В строительстве популярны тавровые балки из МДФ, применяемые в качестве сердечника балок межэтажных перекрытий при монолитном строительстве. Водостойкое МДФ используется для обрешетки крыш — элементы такой обрешетки окрашиваются для более долгой службы масляной краской.
Достоинства МДФ
К достоинствам МДФ относится способность сохранять долгое время геометрические параметры, что позволяет говорить о длительном сроке службы. Изделия из МДФ допускается использовать в помещениях с высокой влажностью воздуха – пропитки сохраняют плиты от развития плесени и грибка, от деятельности насекомых. Тем не менее, панели МДФ не рекомендуются к установке в помещения с постоянно высоким уровнем влажности воздуха, за исключением их водостойких модификаций. МДФ – хороший утеплитель и звуковой изолятор. Можно усилить эти свойства, уложив под него изолирующий материал. Самый большой плюс МДФ — благоприятное соотношение между толщиной и твердостью. Это материал имеет однородную, плотную, ровную, гладкую поверхность, что делает обработку плит быстрой и легкой. Плотность материала составляет от 600 кг/м³ до 800 кг/м³, что немало. Прочность МДФ в 1,8-2 раза выше прочности древесностружечных плит. Благодаря гладкой и твердой поверхности плиты МДФ прекрасно подходят для отделки прогрессивными методами ламинирования, каширования, для фанерования тонким шпоном, имитационной печати, покрытия лаками и эмалями. При наличии необходимых инструментов можно выпилить в панели любые узоры, украсить декоративной вырезкой. При этом исключаются известные недостатки массивной древесины: анизотропность свойств в зависимости от направления древесных волокон, склонность к растрескиванию при изменении температурно-влажностных условий эксплуатации и т. д. МДФ прекрасно раскраивается твердосплавными пилами. При сверлении МДФ используются те же инструменты, которые применяются для фанеры и ДСП. Достигаются отличные результаты при фрезеровании кромок и поверхностей. Структура МДФ гарантирует исключительно высокое качество при высоких скоростях обработки. Для склеивания МДФ подходят все имеющиеся марки клеящих веществ древесины. В процессе производства МДФ можно придавать специальные свойства: огнестойкость, биостойкость, водостойкость. Также стоит отметить относительно невысокую стоимость МДФ. Панели МДФ требуют минимального и простого ухода – достаточно изредка протирать плиты влажной салфеткой или одним из специальных средств, которые сегодня в избытке продаются в магазинах.
Недостатки МДФ
К недостаткам плит МДФ относится их легкая воспламеняемость при контакте с открытым огнем. Также стоит отметить не очень высокую устойчивость к механическим повреждениям: случайное падение тяжелого предмета на поверхность МДФ может оставить вмятину. Что касается работы с МДФ, следует заметить, что вбить гвоздь или вкрутить шуруп в МДФ будет практически невозможно, требуется предварительное высверливание отверстия под крепление. Во время обработки и фрезеровке плит образуется много пыли — обязательно использование респиратора. МДФ плиты имеют на порядок больший вес по сравнению с деревянными плитами такого же размера. Несмотря на заявляемую некоторыми производителями экологичность, это не совсем так. Да, класс эмиссии МДФ низок и практически равен природной древесине, но выделение формальдегида все же присутствует. То есть, хотя МДФ плиты и сравниваются с деревом, но они не настолько экологичные.
МДФ в России
Сегодня на российском рынке листовых строительно-отделочных материалов представлены древесно-волокнистые плиты средней плотности как отечественных, так и зарубежных производителей. Наибольшее распространение получила продукция таких брендов, как: Kronospan (Россия, г. Егорьевск), Kronostar (Россия, г. Шарья), Шекнинский КДП (Россия, Вологодская обл.), Glunz AG (Германия), EGGER (Австрия), Коростеньский завод МДФ (Украина).
berbex.ru
МДФ – это… Что такое МДФ?
МДФ – древесноволокнистая плита средней плотности, МДФ (англ. Medium Density Fiberboard, MDF) — плитный материал, изготавливаемый методом сухого прессования мелкодисперсной древесной стружки при высоком давлении и температуре. В качестве связующего используются карбамидные смолы, модифицированные меламином. В отличие от традиционно применяющимся ДВП плиты МДФ фризируются и покрываются декоративными плёнками.
[Словарь архитектурно-строительных терминов]
Рубрика термина: ДВП
Рубрики энциклопедии: Абразивное оборудование, Абразивы, Автодороги, Автотехника, Автотранспорт, Акустические материалы, Акустические свойства, Арки, Арматура, Арматурное оборудование, Архитектура, Асбест, Аспирация, Асфальт, Балки, Без рубрики, Бетон, Бетонные и железобетонные, Блоки, Блоки оконные и дверные, Бревно, Брус, Ванты, Вентиляция, Весовое оборудование, Виброзащита, Вибротехника, Виды арматуры, Виды бетона, Виды вибрации, Виды испарений, Виды испытаний, Виды камней, Виды кирпича, Виды кладки, Виды контроля, Виды коррозии, Виды нагрузок на материалы, Виды полов, Виды стекла, Виды цемента, Водонапорное оборудование, Водоснабжение, вода, Вяжущие вещества, Герметики, Гидроизоляционное оборудование, Гидроизоляционные материалы, Гипс, Горное оборудование, Горные породы, Горючесть материалов, Гравий, Грузоподъемные механизмы, Грунтовки, ДВП, Деревообрабатывающее оборудование, Деревообработка, ДЕФЕКТЫ, Дефекты керамики, Дефекты краски, Дефекты стекла, Дефекты структуры бетона, Дефекты, деревообработка, Деформации материалов, Добавки, Добавки в бетон, Добавки к цементу, Дозаторы, Древесина, ДСП, ЖД транспорт, Заводы, Заводы, производства, цеха, Замазки, Заполнители для бетона, Защита бетона, Защита древесины, Защита от коррозии, Звукопоглащающий материал, Золы, Известь, Изделия деревянные, Изделия из стекла, Инструменты, Инструменты геодезия, Испытания бетона, Испытательное оборудование, Качество цемента, Качество, контроль, Керамика, Керамика и огнеупоры, Клеи, Клинкер, Колодцы, Колонны, Компрессорное оборудование, Конвеера, Конструкции ЖБИ, Конструкции металлические, Конструкции прочие, Коррозия материалов, Крановое оборудование, Краски, Лаки, Легкие бетоны, Легкие наполнители для бетона, Лестницы, Лотки, Мастики, Мельницы, Минералы, Монтажное оборудование, Мосты, Напыления, Обжиговое оборудование, Обои, Оборудование, Оборудование для производства бетона, Оборудование для производства вяжущие, Оборудование для производства керамики, Оборудование для производства стекла, Оборудование для производства цемента, Общие, Общие термины, Общие термины, бетон, Общие термины, деревообработка, Общие термины, оборудование, Общие, заводы, Общие, заполнители, Общие, качество, Общие, коррозия, Общие, краски, Общие, стекло, Огнезащита материалов, Огнеупоры, Опалубка, Освещение, Отделочные материалы, Отклонения при испытаниях, Отходы, Отходы производства, Панели, Паркет, Перемычки, Песок, Пигменты, Пиломатериал, Питатели, Пластификаторы для бетона, Пластифицирующие добавки, Плиты, Покрытия, Полимерное оборудование, Полимеры, Половое покрытие, Полы, Прессовое оборудование, Приборы, Приспособления, Прогоны, Проектирование, Производства, Противоморозные добавки, Противопожарное оборудование, Прочие, Прочие, бетон, Прочие, замазки, Прочие, краски, Прочие, оборудование, Разновидности древесины, Разрушения материалов, Раствор, Ригеля, Сваи, Сваизабивное оборудование, Сварка, Сварочное оборудование, Свойства, Свойства бетона, Свойства вяжущих веществ, Свойства горной породы, Свойства камней, Свойства материалов, Свойства цемента, Сейсмика, Склады, Скобяные изделия, Смеси сухие, Смолы, Стекло, Строительная химия, Строительные материалы, Суперпластификаторы, Сушильное оборудование, Сушка, Сушка, деревообработка, Сырье, Теория и расчет конструкций, Тепловое оборудование, Тепловые свойства материалов, Теплоизоляционные материалы, Теплоизоляционные свойства материалов, Термовлажносная обработка бетона, Техника безопасности, Технологии, Технологии бетонирования, Технологии керамики, Трубы, Фанера, Фермы, Фибра, Фундаменты, Фурнитура, Цемент, Цеха, Шлаки, Шлифовальное оборудование, Шпаклевки, Шпон, Штукатурное оборудование, Шум, Щебень, Экономика, Эмали, Эмульсии, Энергетическое оборудование
Источник: Энциклопедия терминов, определений и пояснений строительных материалов
Энциклопедия терминов, определений и пояснений строительных материалов. – Калининград. Под редакцией Ложкина В.П.. 2015-2016.
construction_materials.academic.ru
Как определить, что лучше – МДФ или ДСП?
На рынке строительных материалов сейчас представлено огромное количество плит различных модификаций. Чтобы как-то в этом разобраться, попробуем понять суть вопроса. Что лучше — МДФ или ДСП? Нельзя ответить однозначно. По сути, это одна и та же плита, выполненная из древесных стружек и волокон. Отличие может быть в обработке, связующих составах и в отделке.
Своим названием МДФ обязана английскому словосочетанию Medium Density Fiberboard. Появилась она впервые в Америке, поэтому первые буквы были американские. Если делать точный перевод, то MDF – это древесно-волокнистая плита средней плотности. При ее изготовлении в состав массы, из которой она производится, помимо стружки добавляют волокна древесины. ДСП же полностью состоит из прессованной стружки. Но каждый материал имеет свое применение в различных областях нашей жизнедеятельности.
Основой для МДФ и ДСП служат волокна и стружка различных пород дерева. В обработку идут древесные отходы. Это и определяет низкую стоимость материала. Чтобы получилось качественное изделие, стружка проходит несколько этапов обработки. После измельчения она попадает на обработку паром. Здесь же добавляют различные клеевые составляющие. Для образования МДФ используют натуральную смолу в качестве скрепляющего состава, затем вся эта масса идет под горячий пресс. Здесь формируется плита, которая в дальнейшем подвергается шлифованию. При необходимости она проходит следующие этапы обработки. МДФ выпускается нескольких видов. Облагороженная плита может быть покрашена или заламинирована пленкой под любой оттенок. В магазине продаются плиты с отделкой шпоном под имитацию благородного дерева. Стоимость различается от примененного варианта обработки.
Сложно сказать, что лучше — МДФ или ДСП, ведь каждый материал обладает хорошими характеристиками. Правда, от недостатков тоже уйти не удалось. МДФ, благодаря использованию в производстве мебели, стала популярной. Не только фасады, но и столешницы из этого материала прочно обосновались на нашей кухне. Легкость обработки позволяет придавать дверцам любую форму и рисунок филенки, что значительно упрощает изготовление разных мебельных гарнитуров. Широкое применение нашел этот материал в напольных покрытиях, часто используется в строительстве при установке перегородок или утеплении крыш.
ДСП, по сути, является таким же материалом, только с более дешевым заполнением. Эта технология позволяет сделать деревообрабатывающее производство практически безотходным. Стружка прессуется в плиту и обрабатывается. Понять, что лучше – МДФ или ДСП, позволит применение разного материала в одинаковых условиях. В магазинах представлены разные стоимостные группы. Сорт выбираемого материала влияет на цену.
Ламинированное ДСП, цена которого значительно ниже, представляет серьезного соперника в производстве не только мебели, но и напольных покрытий. Пленки имеют гладкую или шероховатую поверхность, поэтому сразу и не отличишь. Но выбирать материал нужно правильно. Плиты ДСП могут быть сверхтвердыми, твердыми, средней плотности и мягкими. При покупке обращайте внимание на направление и размеры стружек. Многослойная плита имеет несколько слоев с разным направлением расположения стружки.
Если вы еще не сделали окончательный выбор и не можете определить, что лучше – МДФ или ДСП, то исходите от тех требований, которые важны на данный момент. Столешница на кухне должна быть из твердого материала, ведь на ней вы будете готовить еду. А дверца шкафчика не несет такую нагрузку, для нее важнее внешний вид, ведь она украшает вашу кухню. Выбирая между МДФ и ДСП, учитывайте стойкость материала к влажности. От этого может зависеть долговечность вашего мебельного гарнитура.
fb.ru